Marine Machinery Regulations
SOR/90-264
Registration 1990-05-01
Regulations Respecting the Construction, Installation and Inspection of Marine Machinery
P.C. 1990-744 1990-04-26
His Excellency the Governor General in Council, on the recommendation of the Minister of Transport, pursuant to section 338Footnote * of the Canada Shipping Act, is pleased hereby to revoke the Liquified Petroleum Gas Regulations, C.R.C., c. 1437, the Steamship Machinery Construction Order, C.R.C., c. 1490, the Steamship Machinery Construction Regulations, C.R.C., c. 1491 and the Steamship Machinery Inspection Regulations, C.R.C., c. 1492, and to make the annexed Regulations respecting the construction, installation and inspection of marine machinery, in substitution therefor.
Return to footnote *R.S., c. 6 (3rd Supp.), s. 47
Short Title
1 These Regulations may be cited as the Marine Machinery Regulations.
Interpretation
2 (1) In these Regulations,
- Act
Act means the Canada Shipping Act; (Loi)
- approved classification society
approved classification society means the American Bureau of Shipping, Bureau Veritas (Canada), Det norske Veritas, Lloyd’s Register of Shipping or Germanischer Lloyd; (société de classification agréée)
- assigned working pressure
assigned working pressure means the maximum fluid pressure to which the component with the lowest design working pressure in a system may be subjected and above which the system is protected from overpressure; (pression de service effective)
- auxiliary steering gear
auxiliary steering gear means the arrangements provided for effecting movement of the rudder of a ship in the event of failure of the main steering gear, but does not include the rudder stock, tiller or quadrant, or the component serving the same purpose as the tiller or quadrant, or, where fitted, the automatic-pilot system; (appareil à gouverner auxiliaire)
- boiler
boiler means a plant that generates steam or hot water under pressure by means of a flame, combustion gases or electrical heating elements, and includes the superheaters, economizers, valves and components necessary for the safety and operation of the plant; (chaudière)
- classification society
classification society means a society or association for the classification of ships; (société de classification)
- component
component means a unit or part of a unit that is identified in rules or codes and is to be installed as part of machinery; (élément)
- component inspection certificate
component inspection certificate means a certificate referred to in section 16; (certificat d’inspection d’élément)
- design working pressure
design working pressure means the maximum fluid pressure to which a component may be subjected during operating conditions; (pression de service nominale)
- fluid
fluid means a gas, vapour or liquid; (fluide)
- fuel oil unit
fuel oil unit means the facility, including pressure pumps, filters and heaters, dealing with oil at a pressure in excess of 180 kPa and used in the preparation of fuel oil for delivery to an oil-fired boiler or, where the oil is heated prior to delivery, to an internal combustion engine; (appareil à mazout)
- harmful substance
harmful substance means waste as defined in the Arctic Waters Pollution Prevention Act or pollutant as defined in section 673 of the Act; (substance nocive)
- inspection certificate
inspection certificate means an inspection certificate referred to in Part V of the Act; (certificat d’inspection)
- inspector
inspector means a person appointed as a steamship inspector pursuant to section 301 of the Act; (inspecteur)
- launch
launch means a ship that has an open cockpit or a cockpit covered by a light trunk cabin in which passengers may be carried; (chaloupe)
- length
length means
(a) in the case of a Safety Convention passenger ship, the horizontal distance measured between perpendiculars erected at the extreme ends of the deepest subdivision load line,
(b) in the case of a ship, other than a Safety Convention passenger ship, that is required to be registered pursuant to the Act,
(i) the distance measured from the fore-part of the uppermost end of the stem to the aft side of the head of the stern post, except that where a stern post is not fitted to the ship, it is the distance from the fore-part of the uppermost end of the stem to the foreside of the head of the rudder stock,
(ii) where the ship has no rudder stock or has a rudder stock situated outside the hull at the stern, the distance measured from the foreside of the foremost permanent structure to the aft side of the aftermost permanent structure of the ship, but not including guards or rubbing strakes, or
(iii) where the ship is a double-ended ship, the distance measured from the aft side of the forward rudder stock to the foreside of the aft rudder stock, and
(c) in the case of a ship that is not required to be registered pursuant to the Act, the horizontal distance measured between perpendiculars erected at the extreme outside ends of the hull; (longueur)
- liquefied petroleum gas
liquefied petroleum gas means a liquefied inflammable gas that is composed predominantly of hydrocarbons or mixtures of hydrocarbons such as propane, propylene, butane, butylene or butadene, and that has a Reid vapour pressure exceeding 276 kPa absolute at 38° C; (gaz de pétrole liquéfié)
- local steering gear control system
local steering gear control system means a system by which required rudder movements are transmitted to the steering gear power unit controls from a position within the steering gear compartment; (système local de commande de 1‘appareil à gouverner)
- machinery spaces
machinery spaces means machinery spaces of category A and all other spaces containing propelling machinery, steering gears, boilers, steam and internal combustion engines, generators and major electrical machinery, oil filling stations, refrigerating, stabilizing, ventilation and air-conditioning machinery, and similar spaces, and trunks to the spaces; (tranche des machines)
- machinery spaces of category A
machinery spaces of category A means
(a) spaces that contain
(i) internal combustion-type machinery used for main propulsion or, where the aggregate of total power output is not less than 373 kW, for purposes other than main propulsion,
(ii) an oil-fired boiler, or
(iii) a fuel oil unit, and
(b) trunks to spaces referred to in paragraph (a); (tranche des machines de catégorie A)
- main steering gear
main steering gear means the main steering gear power unit and actuator by which torque is applied to the rudder stock for the purposes of effecting movement of the rudder to steer a ship; (appareil à gouverner principal)
- major repairs
major repairs means repairs or alterations to machinery that substantially alter the capacity, size or type of the machinery; (réparations majeures)
- material test certificate
material test certificate means a certificate referred to in section 10; (certificat d’essai de matériau)
- periodic general inspection
periodic general inspection means a periodic general inspection described in subsection 19(2); (inspection périodique générale)
- periodic special inspection
periodic special inspection means a periodic special inspection described in subsection 20(1); (inspection périodique spéciale)
- pressure vessel
pressure vessel means a boiler or an unfired pressure vessel; (récipient sous pression)
- remote steering gear control system
remote steering gear control system means the system by which required rudder movements are transmitted to the steering gear power unit controls from the bridge or another location in a ship, excluding the steering gear compartment; (système de commande à distance de l’appareil à gouverner)
- rudder actuator
rudder actuator means a unit transmitting torque to a rudder stock
(a) through an externally connected tiller, quadrant or similar component, or
(b) directly through an integrally housed vane or similar component; (actionneur de gouvernail)
- rules or codes
rules or codes means rules, regulations or codes relating to the construction, installation and inspection of marine machinery, issued by an approved classification society; (règles ou codes)
- shipside door-operating mechanism
shipside door-operating mechanism means machinery employed in the opening and closing of a hull door, visor or roll on/roll off ramp of a ship, but does not include the door, visor or ramp or any locking device; (mécanisme de manoeuvre des portes de muraille)
- steering gear power unit
steering gear power unit means
(a) in the case of an electric steering gear, an electric motor and its associated electrical arrangements,
(b) in the case of an electro-hydraulic steering gear, an electric motor, and its associated electrical arrangements and the connected hydraulic pump, and
(c) in the case of a hydraulic steering gear, the driving engine and connected hydraulic pump; (groupe moteur d’appareil à gouverner)
- test pressure
test pressure means the maximum pressure to which the fluid in a component or system may be subjected during inspection; (pression d’essai)
- unfired pressure vessel
unfired pressure vessel means a container subjected to internal or external pressure, where the pressure is produced without the application of heat from an external source or by the application of heat from an indirect source or by any combination thereof, and includes condensers, evaporators, air receivers, hydro-pneumatic tanks, hydraulic accumulators, heat exchangers and similar components, but does not include cooling or heating spaces of engines, pumps, compressors, piping and similar components; (récipient sous pression non chauffé)
- windlass
windlass means the machinery and arrangements principally employed in the lowering and raising of the anchors of a ship, but does not include the anchors and cables. (guindeau)
(2) The units of measurement used in these Regulations are as defined in the Metric Practice Guide published by the Canadian Standards Association.
(3) Unless specifically stated otherwise, all prescribed pressures are gauge pressures.
- SOR/2002-428, s. 1
Application
3 (1) Subject to subsection (2), these Regulations apply in respect of every ship as defined in Part XV of the Act.
(2) These Regulations do not apply in respect of a pleasure yacht or a non-passenger, non-self-propelled ship, except in respect of
(a) propulsion system boilers on board a pleasure yacht, where the yacht is in excess of five tons gross tonnage; and
(b) boilers and compressed air receivers on board a non-passenger, non-self-propelled ship carrying a crew where the ship
(i) may operate or ply on voyages more than 15 miles from land, or
(ii) does not operate or ply on voyages more than 15 miles from land and the boilers or compressed air receivers have an assigned working pressure in excess of 103 kPa.
Construction and Installation Standards
4 (1) Any machinery referred to in Schedules I to XV that is constructed after the coming into force of these Regulations shall be constructed and installed in a ship in accordance with the following standards or specifications in force at the time the construction is commenced:
(a) the standards or specifications in the rules or codes under which the machinery is being constructed; and
(b) the design specifications set out in each item of Part I of the applicable schedule of Schedules I to XV and the general design specifications set out in Schedule XVI.
(2) In the event of any inconsistency between the standards or specifications referred to in paragraph (1)(a) and the specifications referred to in paragraph (1)(b), the specifications referred to in paragraph (1)(b) shall prevail.
(3) Any machinery referred to in subsection (1) that has been constructed in accordance with the standards or specifications in rules or codes of an approved classification society may be installed in a ship in accordance with the rules or codes of another approved classification society.
5 (1) Subject to subsection (2), major repairs to machinery referred to in Schedules I to XV that was constructed before or after the coming into force of these Regulations, including the reinstallation of components associated with the machinery following the major repairs, shall be made in accordance with the standards or specifications referred to in subsection 4(1) in force at the time the major repairs are commenced.
(2) Where making major repairs in accordance with subsection (1) would be impracticable or inappropriate, the major repairs may be made in accordance with the standards or specifications relating to construction set out in the regulations in force at the time construction of the machinery commenced.
Plans
6 (1) Subject to subsection (5), plans of machinery referred to in Schedules I to XV required by these Regulations to be inspected shall be submitted to the Board prior to the commencement of any inspection.
(2) Where machinery is constructed or installed after the coming into force of these Regulations, the plans shall be submitted to the Board prior to the commencement of construction or installation of the machinery, as the case may be.
(3) The plans shall
(a) be in quadruplicate unless the Board specifies that fewer than four plans are required, in English or French and in fully dimensioned form;
(b) include the information set out in each item of Part II of the applicable schedule of Schedules I to XV;
(c) indicate the approved classification society in accordance with the rules or codes of which the machinery will be or was constructed or installed; and
(d) reflect the standards and specifications referred to in subsection 4(1).
(4) The Board may require that additional information referred to in Part II of the applicable schedule of Schedules I to XV be included in the plans.
(5) The plans need not be submitted to the Board if plans that conform to these Regulations for identical machinery have previously been submitted to the Board.
(6) The submitted plans shall be inspected by an inspector and where the plans meet the requirements set out in paragraphs (3)(a) to (d) and subsection (4) shall be stamped to indicate that the plans comply with those requirements.
- SOR/2015-161, s. 3(F)
Material Testing and Marking
7 Specimen pieces of any material to be used in the construction of or repairs to machinery referred to in subsection 4(1) and required by the rules or codes under which the machinery is to be constructed to be tested prior to use shall be identified and shall, in the presence of an inspector, undergo, prior to the commencement of construction or repairs, the tests set out in those rules or codes.
- SOR/2015-161, s. 4
8 (1) An inspector referred to in section 7 shall, prior to the commencement of a test, be provided with evidence that shows that all the material testing equipment to be used is in correct operational condition and adjustment.
(2) The evidence referred to in subsection (1) may consist of current reports or certificates issued by an equipment testing organization that is accredited by the Standards Council of Canada.
9 On completion of the tests in the presence of an inspector, referred to in section 7, the material shall be permanently marked in the presence of that inspector with
(a) the information on the material test certificate set out in Schedule XVII under the heading “MARKING — MARQUES”; and
(b) the Federal Identity Symbol as printed on a stamp provided by the inspector.
10 An inspector shall issue a material test certificate in respect of a material in the form set out in Schedule XVII where
(a) the specimen pieces of the material meet the test requirements set out in the rules or codes referred to in section 7; and
(b) the material has been marked in accordance with section 9.
11 (1) Notwithstanding sections 7 and 9, an exclusive surveyor to an approved classification society or a metallurgist certified by a provincial government or by any other authority having similar certification standards may witness the tests and marking referred to in those sections.
(2) Where an exclusive surveyor or metallurgist referred to in subsection (1) witnesses the tests and marking of a material,
(a) the material test certificate shall include all testing information, bear the identification symbol of the employer of the exclusive surveyor or metallurgist and be signed by the exclusive surveyor or metallurgist; and
(b) the permanent marking on the material shall include the identification symbol of the employer of the exclusive surveyor or metallurgist.
Construction and Installation Inspections
12 (1) Subject to section 15, all machinery referred to in subsections 4(1) and 5(1) shall be inspected by an inspector during construction, installation and major repair.
(2) An inspection referred to in subsection (1) shall consist of the completion of each item set out in Part III of the applicable schedule of Schedules I to XV.
13 No inspection of machinery shall be carried out unless the tests and marking referred to in sections 7 to 9 have been completed and the material test certificates referred to in section 10 or 11 have been provided to the inspector.
14 No pressure vessel referred to in Schedules I to III shall be inspected unless the following conditions have been met:
(a) the manufacturer’s construction and testing facilities have, prior to the commencement of construction of the pressure vessel in accordance with these Regulations, been inspected by an inspector and the inspector has submitted a report thereon to the Board; and
(b) the Board has determined on the basis of the report that the facilities are, in accordance with the state of the art, suitable for the construction or testing of boilers or unfired pressure vessels of Class 1, 2 or 3, as the case may be.
15 (1) No inspection of standardized and mass-produced machinery is required where
(a) the manufacturer has established and continuously applied, throughout the construction and testing of the machinery, quality control procedures that meet the requirements of paragraphs (2)(b) and (c); and
(b) the manufacturer provides to the Board in respect of the machinery the following documentary information:
(i) the model and serial number of the machinery,
(ii) confirmation that materials testing was carried out and that the materials meet the requirements of the rules or codes under which the machinery was constructed,
(iii) confirmation that the machinery was constructed in accordance with these Regulations,
(iv) confirmation that the machinery was tested in accordance with these Regulations on completion of the construction, and
(v) the permanent identification marking of the manufacturer and the location of the marking on the machinery.
(2) The Board may approve the quality control procedures of a manufacturer where
(a) the manufacturer has submitted to the Board full documentation covering the quality control procedures being applied, including periodic auditing arrangements;
(b) the quality control procedures and the construction and testing facilities have been inspected
(i) by an inspector and the inspector has submitted a report thereon to the Board, or
(ii) by an exclusive surveyor to an approved classification society and the surveyor has submitted a report thereon to the approved classification society, the society has accepted the report and issued an acceptance certificate in respect of the inspection and a copy of the certificate has been submitted to the Board; and
(c) the Board has determined on the basis of the documentation submitted that the manufacturer’s facilities and quality control procedures are, in accordance with the state of the art, suitable for the construction and testing of the machinery.
Component Inspection Certificate and Marking
16 Subject to section 17, where an inspector has carried out a construction inspection of machinery in accordance with subsection 12(2), the inspector shall issue a component inspection certificate in the form set out in Schedule XVIII for each component of that machinery that is constructed in accordance with these Regulations.
17 Before issuing a component inspection certificate, an inspector shall ensure that the component is marked with the information on the certificate referred to in section 16 under the heading “MARKING — MARQUES”, including the Federal Identity Symbol.
18 (1) The marking referred to in section 17 shall be conspicuous and not readily effaced, covered or removed, and shall be located
(a) in the case of a hot-water boiler or a steam boiler, adjacent to an access or visual inspection opening;
(b) in the case of an unfired pressure vessel, on an end plate;
(c) in the case of a shaft, on the flange rim;
(d) in the case of a propeller, on the hub; and
(e) in the case of any other component, adjacent to the manufacturer’s permanent identification marking.
(2) Where a component cannot be marked on a location referred to in subsection (1) because marking on the location would be physically impossible or unsafe or the marking would not be readily visible, the inspector may accept another suitable location for the marking.
Periodic General Inspections and Periodic Special Inspections
19 (1) No inspection, other than an inspection referred to in sections 24 and 25, shall be carried out pursuant to section 316 of the Act unless a component inspection certificate has been issued for each component.
(2) Where machinery referred to in Schedules I to XV is subject to an inspection referred to in subsection (1) at one year or four year intervals, an inspector shall carry out a periodic general inspection that consists of an external inspection of the machinery comprising an inspection or the completion of each item set out in Division I of Part IV of the applicable schedule of Schedules I to XV.
20 (1) Machinery referred to in Schedules I to XV is subject to a periodic special inspection by an inspector in accordance with subsection (2) and shall consist of an external and an internal inspection of the machinery comprising an inspection of each item set out in Subdivision I of Division II of Part IV of the applicable schedule of Schedules I to XV.
(2) Periodic special inspections shall be carried out
(a) at the intervals set out in Subdivision II of Division II of Part IV of the applicable schedule of Schedules I to XV; and
(b) at the time of the periodic general inspection, where during the periodic general inspection the inspector has reasonable grounds to believe that there are internal defects in the machinery.
21 Where a periodic special inspection is required in accordance with paragraph 20(2)(a), a periodic general inspection shall be carried out, as soon as practicable, subsequent to the reassembly of the machinery that was inspected.
22 Where machinery is to be inspected in accordance with these Regulations, the ship owner shall ensure that the machinery is opened up and cleaned and the removable components are removed, as required by the inspector.
Continuous Periodic Special Inspections
23 (1) On a written request to the Board by a ship owner, the Board may approve a system of continuous periodic special inspections where the inspection requirements referred to in paragraph 20(2)(a) are complied with according to a cycle in which approximately the same number of components is inspected in each 12-month period.
(2) An up-to-date record indicating the status of the continuous periodic special inspection of the various components on board a ship shall be maintained by the Board and a copy of the record shall be forwarded to the ship or owner of the ship, on request.
(3) Where, in the course of a continuous periodic special inspection, a defect is found in a component and the nature of the defect and the operational conditions indicate that there may be a similar defect in a related or similar component on board the ship, the inspector may require that the related or similar component also be inspected during the inspection.
Foreign Machinery
24 (1) Subject to subsection (3), machinery referred to in Schedules I to XV that is installed in a foreign ship which ship has never been registered in Canada and is registered in Canada for the first time after the coming into force of these Regulations shall, prior to the ship’s service as a Canadian ship, be subject to a first periodic general inspection and a first periodic special inspection.
(2) Subject to subsection (3), machinery referred to in Schedules I to XV that is constructed in a foreign country and is brought into Canada for installation in a Canadian ship shall be subject to a first periodic general inspection and a first periodic special inspection prior to its use.
(3) A first periodic special inspection of any machinery referred to in subsections (1) and (2) is not required where
(a) a certificate is submitted to the Board showing
(i) that the construction and, as applicable, the installation of the machinery were inspected by an exclusive surveyor to an approved classification society,
(ii) that the machinery conforms to the rules or codes under which the machinery was constructed that were in force at the time the machinery was constructed, and
(iii) the form and location of identification symbols of the approved classification society on the machinery;
(b) in the case of machinery that has been installed in a ship, valid certificates of periodic class survey by an exclusive surveyor to an approved classification society are submitted to the Board;
(c) the inspector determines, on the basis of the first periodic general inspection,
(i) in the case of machinery referred to in subsection (1), that the machinery conforms to standards and specifications set out in regulations in force at the time the machinery was constructed, and
(ii) in the case of machinery referred to in subsection (2), that the machinery conforms to design specifications set out in regulations in force at the time the machinery was constructed; and
(d) in the case of a pressure vessel, certificates of an approved classification society under the rules and codes of which the pressure, vessel was constructed, showing that the manufacturer’s construction and testing facilities were in compliance with those rules or codes, are submitted to the Board.
(4) Where a first periodic special inspection is not required pursuant to subsection (3), a periodic special inspection shall be carried out on the due date of the next periodic special survey of the approved classification society under which the ship is classed.
(5) Notwithstanding subsection 6(1), a first periodic general inspection of machinery referred to in subsection (1) may take place prior to submission of the plans of the machinery where the applicable certificates referred to in subsection (3) have been submitted to the Board.
(6) Plans of machinery referred to in subsection (1) shall be submitted to the Board on a day that is not later than three months prior to the first periodic special inspection of the machinery.
(7) Where, in accordance with paragraph (3)(a), a certificate has been submitted to the Board and the machinery bears the identification symbol of the approved classification society, the component inspection certificate set out in Schedule XVIII is not required to be issued.
25 (1) Subject to subsections (2) and (3), machinery referred to in Schedules I to XV that is installed in a foreign ship that was previously registered in Canada before the coming into force of these Regulations and is re-registered in Canada after the coming into force of these Regulations shall be subject to a periodic general inspection and a periodic special inspection.
(2) The periodic special inspection referred to in subsection (1) is not required where
(a) the inspector determines on the basis of the periodic general inspection that the machinery conforms to standards and specifications set out in regulations in force at the time the machinery was constructed; and
(b) valid certificates of periodic class survey by an exclusive surveyor to an approved classification society are submitted to the Board.
(3) Where a periodic special inspection is not required pursuant to subsection (2), a periodic special inspection shall be carried out on the due date of the next periodic special survey of the approved classification society under which the ship is classed.
SCHEDULE ISteam Boilers Having a Design Working Pressure Exceeding 350 kPa
PART I(Section 4)Design Specifications
Item | Requirements |
---|---|
1 | None. |
PART II(Section 6)Plans
Item | Required Information |
---|---|
1 | General arrangement of the installation of the steam boiler in the ship showing means of support. |
2 | Design working pressure, temperature and evaporation rate. |
3 | Heating surface area of the steam boiler, and where fitted, of the superheater and economizer. |
4 | Materials, sizes and arrangement of parts under pressure, including superheaters, economizers and valves. |
5 | Details of welded seams, openings, connections, attachments and supports, including details of welding materials, methods and procedures. |
6 | Details of the heat treatment process and testing procedures. |
7 | Pressure setting, relieving capacity and venting arrangements of safety valves. |
8 | Arrangements and details of steam boiler feed-water controls, monitors and alarms, including emergency controls. |
9 | Materials, components, sizes and arrangements of fuel combustion systems, including fuel supply, combustion air supply, air preheaters, exhaust uptakes and combustion controls, monitors and alarms, including emergency controls. |
PART III(Subsection 12(2))Construction and Installation Inspections
DIVISION IConstruction Inspection
Item | Requirements |
---|---|
1 | Identification from material test certificates, before construction is commenced, of materials to be used, including welding metal, and of physical properties and mechanical test results obtained from material testing carried out in accordance with these Regulations. |
2 | Verification that welding was carried out by welders certified by a Provincial Government of Canada, or another authority having similar standards where the welding was carried out outside Canada, for the class of work to be done. |
3 | Inspection of welds including non-destructive test examination and verification of the heat treatment process in accordance with rules or codes. |
4 | Verification of plate preparation and alignment prior to assembly and, on completion of all construction operations, confirmation of circularity of shells. |
5 | Identification from the component inspection certificates of components related to the safety of the boiler. |
6 | Inspection of components and their installation, including tubes and tube plates. |
7 | Inspection of the constructed steam boiler. |
8 | Witnessing of hydrostatic pressure tests in accordance with rules or codes. |
DIVISION IIInstallation Inspection
Item | Requirements |
---|---|
1 | Verification of correct alignment of securing arrangements. |
2 | Verification of correct adjustment and operational condition of the connection of the steam boiler to steam, feed-water, blowdown and surface blow systems. |
3 | Verification of correct adjustment and operational condition of fuel, combustion air supply and exhaust gas systems, including burners, air fans and air preheaters. |
4 | Verification of correct adjustment and operational condition of safety, control and monitoring devices. |
5 | Inspection of safety valve relieving capacity in respect of the maximum evaporation capacity of the steam boiler. |
6 | Witnessing of hydrostatic pressure tests at the assigned working pressure. |
7 | Verification of reliability and sufficiency under trials up to full power under normal working conditions for a suitable endurance period of not less than 2 hours, taking into consideration the size and complexity of the steam boiler. |
PART IVPeriodic General Inspections and Periodic Special Inspections
DIVISION I(Section 19)Periodic General Inspection
Item | Requirements |
---|---|
1 | Correct adjustment and operational condition of safety valves. |
2 | Correct adjustment and operational condition of water gauges and steam boiler valves. |
3 | Locations where fluid leakage, metal overheating or metal wastage may occur. |
4 | Correct adjustment and operational condition of emergency fuel shut-off valves. |
5 | Correct adjustment of controls and monitoring systems of feed-water and fuel and its combustion. |
6 | Operational condition of alarm systems, particularly where the boiler is designed for non-continuous local supervision. |
DIVISION IIPeriodic Special Inspection
SUBDIVISION I(Subsection 20(1))Parts to be Inspected
Item | Requirements |
---|---|
1 | Internal steam and liquid spaces, as far as practicable, of the boiler, superheater and economizer, with all spaces cleaned and removable components removed and where, due to construction features, an adequate internal inspection cannot be carried out, a hydrostatic pressure test of 1.25 times the assigned working pressure of the boiler. |
2 | Access and inspection openings. |
3 | Boiler mountings, including safety valves and water-level gauges, following opening up and cleaning. |
4 | Float chambers and float mechanisms on feed-water regulators, following opening up and cleaning. |
5 | Pipes, actuators and other components, incorporated in self regulating and monitoring systems, as far as practicable, without dismantling if the general condition of the component shows that it is suitable for further service. |
6 | Emergency fuel shut-off devices. |
7 | Combustion spaces following cleaning, excluding uptakes and air preheaters unless there is apparent damage, improper operation or deteriorated condition of the uptakes or air preheaters. |
8 | Seams, mountings, seatings, rolling stays, collision chocks and welded attachments, following the removal of insulation and sheathing to the extent considered necessary by the inspector on the basis of the general condition of the boiler. |
9 | Plate thickness testing or hydrostatic pressure testing or other non-destructive testing, if there is apparent damage, improper operation or deteriorated condition of the boiler. |
SUBDIVISION II(Subsection 20(2))Intervals
Item | Requirements |
---|---|
1 | Combustion air fans and driving components, at intervals not exceeding 5 years and all other components, at intervals not exceeding 24 months. |
SCHEDULE IILow-Pressure Steam Boilers Having a Design Working Pressure Not Exceeding 350 kPa and Hot-Water Boilers Having a Design Working Pressure Not Exceeding 1 100 kPa or a Design Temperature Not Exceeding 120°C
PART I(Section 4)Design Specifications
Item | Requirements |
---|---|
1 | None. |
PART II(Section 6)Plans
Item | Required Information |
---|---|
1 | General arrangement of the installation of the boiler in the ship, showing means of support. |
2 | Design working pressure, temperature and evaporation rate for steam or flow rate for water. |
3 | Heating surface area of the boiler. |
4 | Materials, sizes and arrangements of parts under pressure, including valves. |
5 | Details of welded seams, openings, connections, attachments and supports, including details of welding materials, methods and procedures. |
6 | Pressure setting, relieving capacity and venting arrangement of safety valves. |
7 | Arrangements and details of boiler feed-water controls, monitors and alarms, including emergency controls. |
8 | Diagrammatic arrangements of fuel supply, combustion air supply, combustion controls, monitors and alarms, including emergency controls and a written description of the combustion controls. |
9 | Where a manufacturer of a boiler certifies that the boiler was constructed in accordance with rules or codes, information set out in items 2 to 7 is not required to be submitted
|
PART III(Subsection 12(2))Construction and Installation Inspections
DIVISION IConstruction Inspection
Item | Requirements |
---|---|
1 | Identification from material test certificates, before construction is commenced, of materials to be used, including welding metal, and of physical properties and mechanical test results obtained from material testing carried out in accordance with these Regulations. |
2 | Verification that welding was carried out by welders certified by a Provincial Government of Canada, or another authority having similar standards where the welding was carried out outside Canada, for the class of work to be done. |
3 | Inspection of welds, including non-destructive test examination and verification of the heat treatment process in accordance with rules or codes. |
4 | Verification of plate preparation and alignment prior to assembly and, on completion of all construction operations, confirmation of circularity of shells of the low-pressure steam boiler or of the hot-water boiler. |
5 | Identification from the component inspection certificates of components related to the safety of the low-pressure boiler. |
6 | Inspection of components and their installation, including tubes and tube plates. |
7 | Inspection of the constructed low-pressure boiler. |
8 | Witnessing of an hydrostatic pressure test in accordance with rules or codes. |
DIVISION IIInstallation Inspection
Item | Requirements |
---|---|
1 | Verification of correct alignment of securing arrangements. |
2 | Verification of correct adjustment and operational condition of the connection of the boiler to associated systems. |
3 | Verification of correct adjustment and operational condition of safety, control and monitoring devices. |
4 | Witnessing of hydrostatic pressure tests at the assigned working pressure. |
5 | Verification of reliability and sufficiency under trials up to full power under normal working conditions for a suitable endurance period of not less than 2 hours, taking into consideration the size and complexity of the boiler. |
PART IVPeriodic General Inspections and Periodic Special Inspections
DIVISION I(Section 19)Periodic General Inspection
Item | Requirements |
---|---|
1 | Correct adjustment and operational condition of safety valves. |
2 | Operational condition of water gauges and boiler valves. |
3 | Locations where fluid leakage, metal overheating or metal wastage may occur. |
4 | Correct adjustment and operational condition of emergency fuel shut-off valves. |
5 | Correct adjustment of controls and monitoring systems of feed-water and fuel and its combustion. |
6 | Operational condition of alarm systems, particularly where the boiler is designed for non-continuous local supervision. |
DIVISION IIPeriodic Special Inspection
SUBDIVISION I(Subsection 20(1))Parts to be Inspected
Item | Requirements |
---|---|
1 | Internal steam and liquid spaces, as far as practicable, with all spaces cleaned and removable components removed and where, due to construction features, an adequate internal inspection cannot be carried out, a hydrostatic pressure test of 1.25 times the assigned working pressure of the boiler. |
2 | Access and inspection openings. |
3 | Boiler mountings, including safety valves and water-level gauges, following opening up and cleaning. |
4 | Float chambers and float mechanisms on feed-water regulators, following opening up and cleaning. |
5 | Pipes, actuators and other components, incorporated in self-regulating and monitoring systems, as far as practicable, without dismantling, where the general condition of the pipes, actuators and other components is adequate for further use. |
6 | Emergency fuel shut-off devices. |
7 | Combustion spaces following cleaning, excluding uptakes unless there is apparent damage, improper operation or deteriorated condition of the uptakes. |
8 | Seams, mountings, seatings and welded attachments, following the removal of insulation and sheathing to the extent considered necessary by the inspector on the basis of the general condition of the boiler. |
9 | Plate thickness testing or hydrostatic pressure testing or other non-destructive testing, if there is apparent damage, improper operation or deteriorated condition of the boiler. |
10 | Except where, on the basis of the periodic general inspection, there is apparent damage, improper operation or deteriorated condition of components, items 1 to 9 do not apply to
|
SUBDIVISION II(Subsection 20(2))Intervals
Item | Requirements |
---|---|
1 | At intervals not exceeding 24 months. |
SCHEDULE IIIUnfired Pressure Vessels
PART I(Section 4)Design Specifications
Item | Requirements |
---|---|
1 | None. |
PART II(Section 6)Plans
Item | Required Information |
---|---|
1 | General arrangement of the installation of the unfired pressure vessel in the ship, showing means of support. |
2 | Design working pressure, temperature, volume and nature of fluid under pressure. |
3 | Materials, sizes and arrangement of parts under pressure, including valves. |
4 | Details of welded seams, openings, connections, attachments and supports, including details of welding materials, methods and procedures. |
5 | Details of the heat treatment process and testing procedures. |
6 | Diagrammatic arrangement and a written description of the pressure source and heat exchange, as applicable, including cut-offs and alarms. |
7 | Pressure setting, relieving capacity and venting arrangements of safety or liquid relief valves. |
8 | Details of fusible plugs or similar devices required to protect vessels from over-pressure caused by fire or other heat hazards. |
9 | Where a manufacturer of an unfired pressure vessel or a hydro-pneumatic tank certifies that the unfired pressure vessel or hydro-pneumatic tank was constructed in accordance with rules or codes, information set out in items 2 to 8 is not required to be submitted for
|
PART III(Subsection 12(2))Construction and Installation Inspections
DIVISION IConstruction Inspection
Item | Requirements |
---|---|
1 | Identification from material test certificates, before construction is commenced, of materials to be used, including welding metal, and of physical properties and mechanical test results obtained from material testing carried out in accordance with these Regulations. |
2 | Verification that welding was carried out by welders certified by a Provincial Government of Canada, or another authority having similar standards where the welding was carried out outside Canada, for the class of work to be done. |
3 | Inspection of welds including non-destructive test examination and verification of the heat treatment process in accordance with rules or codes. |
4 | Verification of plate preparation and alignment prior to assembly and, on completion of all construction operations, confirmation of circularity of shells. |
5 | Identification from component inspection certificates of components related to the safety of the unfired pressure vessel. |
6 | Inspection of components and their installation, including tubes and tube plates. |
7 | Inspection of the constructed unfired pressure vessel. |
8 | Witnessing of hydrostatic pressure tests in accordance with rules or codes. |
DIVISION IIInstallation Inspection
Item | Requirements |
---|---|
1 | Verification of correct alignment of securing arrangements. |
2 | Verification of correct adjustment and operational condition of the connection of the unfired pressure vessel to associated systems. |
3 | Verification of correct adjustment and operational condition of safety, control and monitoring devices. |
4 | Verification of reliability and sufficiency under trials up to the assigned working pressure under normal working conditions for a suitable endurance period, taking into consideration the size and complexity of the unfired pressure vessel and its pressure source. |
PART IVPeriodic General Inspections and Periodic Special Inspections
DIVISION I(Section 19)Periodic General Inspection
Item | Requirements |
---|---|
1 | Correct adjustment and operational condition of safety devices. |
2 | Operational condition of liquid gauges and attached valves. |
3 | Locations where fluid leakage, metal wastage or metal deformation may occur. |
4 | Correct adjustment of controls and monitoring systems. |
5 | Operational condition of alarm systems, particularly where the unfired pressure vessel is designed for non-continuous local supervision. |
DIVISION IIPeriodic Special Inspection
SUBDIVISION I(Subsection 20(1))Parts to be Inspected
Item | Requirements |
---|---|
1 | Internal fluid spaces as far as practicable with all spaces clean and removable components removed and where, due to construction features, an adequate internal inspection cannot be carried out, a hydrostatic pressure test of 1.25 times the assigned working pressure of the spaces. |
2 | Access and inspection openings and fusible plugs where fitted. |
3 | Pressure-vessel mountings, including safety valves and liquid-level gauges, without opening up and cleaning unless there is apparent damage, improper operation or deteriorated condition of those components. |
4 | Float chambers and float mechanisms on liquid-level regulators, following opening up and cleaning. |
5 | Pipes, actuators and other components, incorporated in self-regulating and monitoring systems, as far as is practicable, without dismantling where their general condition shows that they are suitable for further service. |
6 | Seams, mountings, seatings and welded attachments, following the removal of insulation and sheathing, to the extent considered necessary by the inspector, on the basis of the general condition of the unfired pressure vessel. |
7 | Except where, on the basis of the periodic general inspection, there is apparent damage, improper operation or deteriorated condition of components, items 1 to 6 do not apply where
|
SUBDIVISION II(Subsection 20(2))Intervals
Item | Requirements |
---|---|
1 | Steam-heated steam generators, at intervals not exceeding 2 years. |
2 | Water evaporators and steam condensers, at intervals not exceeding 5 years. |
3 | Unfired pressure vessels containing air or air and water under pressure, at intervals not exceeding 5 years. |
4 | Unfired pressure vessels containing non-corrosive liquid or non-corrosive liquid and gas under pressure, at intervals not exceeding 20 years. |
5 | Liquid tubular heat exchangers with one fluid side opened up, at intervals not exceeding 5 years, and without further dismantling unless dismantling is considered necessary by the inspector on the basis of the general condition of the heat exchangers. |
SCHEDULE IVReciprocating Engines
PART I(Section 4)Design Specifications
DIVISION IInternal Combustion Oil Engines
Item | Requirements |
---|---|
1 | None. |
DIVISION IISteam Reciprocating Engines
Item | Requirements |
---|---|
1 | None. |
PART II(Section 6)Plans
DIVISION IInternal Combustion Oil Engines
Item | Required Information |
---|---|
1 | General arrangement of the installation of the engine in the ship, showing all connected systems. |
2 | General arrangement and sectional elevation of the engine, including crankcase doors and means of engine support. |
3 | Specifications indicating maximum continuous brake power and corresponding revolutions per minute, number of strokes per cycle, number and firing order of cylinders, bore and stroke dimensions, maximum and mean indicated pressures, full details of balance weights, full details of flywheel and physical properties of the principal parts. |
4 | Details of pressure charging, scavenging and exhaust arrangements including mechanisms, piping and pipe connections, type and amount of insulation and method of securing to allow for thermal expansion and vibration. |
5 | Details of all cylinders, cylinder covers, pistons, piston rods, connecting rods and bearings and of the crankshaft and bedplate. |
6 | Details of the fuel injection system. |
7 | Details of lubricating-oil, cooling-water and other attached pumping systems. |
8 | Details of starting arrangements. |
9 | Details of controls including reversing arrangements. |
10 | Details of speed-regulating governors and other safety devices. |
11 | Details of temperature-monitoring devices. |
12 | Details of crankcase venting, crankcase explosion relief valves and other protection devices. |
13 | Details of engine turning gear. |
14 | Torsional vibration analysis of shafting system. |
15 | Information set out in items 2 to 14 is not required to be submitted for the following internal combustion oil engines, namely, an engine
|
DIVISION IISteam Reciprocating Engines
Item | Required Information |
---|---|
1 | General arrangement of the installation of the engine in the ship, showing all connected systems. |
2 | General arrangement and sectional elevation of the engine and means of support. |
3 | Specifications showing the indicated power and corresponding revolutions per minute, number of cylinders, bore and stroke dimensions, maximum pressure per cylinder, full details of flywheel and physical properties of principal parts. |
4 | Details of all cylinders, cylinder covers, pistons, piston rods, connecting rods and bearings and of the crankshaft and bedplate. |
5 | Details of lubricating oil systems and other attached pumping systems. |
6 | Details of controls, including reversing arrangements. |
7 | Details of speed-regulating governors and other safety devices. |
8 | Details of crankcase venting. |
9 | Details of engine turning gear. |
10 | Where a manufacturer of a steam reciprocating engine certifies that the engine was constructed in accordance with rules or codes, information set out in items 2 to 9 is not required to be submitted for the steam reciprocating engine if it is not in excess of 375 kW continuous brake power. |
PART III(Subsection 12(2))Construction and Installation Inspections
DIVISION IConstruction Inspection
Item | Requirements |
---|---|
1 | Identification from material test certificates, before construction is commenced, of materials to be used, including welding metal, for the following parts:
|
2 | Verification that welding was carried out by welders certified by a Provincial Government of Canada, or another authority having similar standards where the welding was carried out outside Canada, for the class of work to be done. |
3 | Inspection of welds including non-destructive test examination and verification of any heat treatment required in accordance with rules or codes. |
4 | Identification of components from component inspection certificates and inspection of components and their installation, including engine-driven pumps. |
5 | Witnessing of hydrostatic pressure tests of components in accordance with rules or codes. |
6 | Inspection of the constructed engine and witnessing of the engine under test. |
DIVISION IIInstallation Inspection
Item | Requirements |
---|---|
1 | Verification of correct alignment of securing arrangements. |
2 | Verification of correct adjustment and operational condition of the connection of the engine to associated systems. |
3 | Verification of correct adjustment and operational condition of safety, control and monitoring devices. |
4 | Verification of reliability and sufficiency under trials up to full power under normal working conditions for a suitable endurance period of not less than 2 hours, taking into consideration the size and the complexity of the steam reciprocating engine or the internal combustion oil engine. |
PART IVPeriodic General Inspections and Periodic Special Inspections
DIVISION I(Section 19)Periodic General Inspection
Item | Requirements |
---|---|
1 | Operational condition of the engine. |
2 | Correct adjustment and operational condition of safety devices. |
3 | Locations where fluid leakage, metal wastage, overheating, heavy vibration or excessive bearing clearances may occur. |
4 | Correct adjustment of controls and monitoring systems. |
5 | Operational condition of alarm systems. |
DIVISION IIPeriodic Special Inspection
SUBDIVISION I(Subsection 20(1))Parts to be Inspected
Item | Requirements |
---|---|
1 | Crankcase, crankshaft, bearings and bolts. |
2 | Pistons, piston rods, connecting rods, guides, cross-heads, bearings and bolts except that removal of thrust bearing components that are an integral part of an engine is not required if tolerances meet the manufacturer’s specifications and there is no apparent damage or deterioration. |
3 | Cylinders, covers, valves, and valve mechanisms. |
4 | Crankcase doors, explosion relief devices and other safety devices. |
5 | Crankcase venting arrangement. |
6 | Pressure charging, scavenging and exhaust systems for internal combustion oil engines. |
7 | Attached pumps. |
8 | Starting mechanisms and clutch gears for internal combustion oil engines. |
9 | Reversing and speed-regulating mechanisms. |
10 | Bedplate, engine structure and fastenings, without dismantling if a general examination indicates that the condition of the components is adequate for further service. |
11 | No periodic special inspection is required for speed-regulating governors and other complex mechanisms, where written information is provided to the inspector by firms specializing in the reconditioning of these parts indicating that the parts are in good order and adjustment. |
12 | For an internal combustion engine not in excess of 450 kW continuous brake power, the removal of pistons and dismantling of bearings is not required if examination of the cylinder cover and crankcase indicates that the condition of the engine is adequate for further service. |
SUBDIVISION II(Subsection 20(2))Intervals
Item | Requirements |
---|---|
1 | For steam reciprocating engines, at intervals not exceeding 5 years. |
2 | Subject to item 3, for internal combustion oil engines, at intervals of not more than 5 years. |
3 | For internal combustion oil engines on the following ships, namely,
after completion of the manufacturer’s recommended running hours but at intervals of not less than 5 years, on the basis of documentary evidence presented to the inspector, or at intervals of 8 years, whichever comes first, if, where the periodic general inspection is carried out annually, at the fifth and subsequent periodic general inspections the engine is in good order based on
|
- SOR/2015-161, ss. 5, 6(F)
SCHEDULE VTurbine Engines
PART I(Section 4)Design Specifications
DIVISION ISteam Turbine Engines
Item | Requirements |
---|---|
1 | None. |
DIVISION IIGas Turbine Engines
Item | Requirements |
---|---|
1 | None. |
PART II(Section 6)Plans
DIVISION ISteam Turbine Engines
Item | Required Information |
---|---|
1 | General arrangement of the installation of the engine in the ship, showing all connected systems. |
2 | General arrangement and sectional elevation of the engine and means of support. |
3 | Specifications for ahead and astern turbines indicating maximum continuous brake power and corresponding revolutions per minute, steam pressures and temperatures at turbine inlet and exhaust, full details of cylinders, rotors, nozzles, blades, couplings and clutches, full details of physical properties of principal parts, details of forgings, castings and weldments, details of the heat treatment process and testing procedures. |
4 | Details of bearings and lubricating oil systems. |
5 | Details of controls including reversing arrangements. |
6 | Details of speed-regulating governors, lubricating oil failure-protection arrangements and other safety devices. |
7 | Details of engine turning gear. |
8 | Details of critical speeds of rotating assemblies including vibration analyses. |
DIVISION IIGas Turbine Engines
Item | Required Information |
---|---|
1 | General arrangement of the installation of the engine in the ship, showing all connected systems. |
2 | General arrangement and sectional elevation of the engine and means of support. |
3 | Specifications of the turbine and compressor indicating maximum continuous brake power and corresponding revolutions per minute, gas pressures and temperatures, full details of casings, combustion chambers, rotors, nozzles, blades, heat exchangers, couplings and clutches, full details of physical properties of principal parts, details of forgings, castings and weldments, details of the heat treatment process and testing procedures. |
4 | Details of fuel system including fuel oil viscosities required for starting and running. |
5 | Details of air inlet and exhaust arrangements. |
6 | Details of controls including means of starting and of fuel ignition. |
7 | Details of bearings and of lubricating oil systems. |
8 | Details of speed-regulating governors, lubricating oil failure protection arrangements and other safety devices. |
9 | Details of engine turning gear. |
10 | Details of critical speeds of rotating assemblies including vibration analyses. |
11 | Information set out in items 1 to 10 is not required to be submitted for
|
PART III(Subsection 12(2))Construction and Installation Inspections
DIVISION IConstruction Inspection
Item | Requirements |
---|---|
1 | Identification from material test certificates, before construction is commenced, of materials to be used, including welding metal, for the following parts:
|
2 | Verification that welding was carried out by welders certified by a Provincial Government of Canada, or another authority having similar standards where the welding was carried out outside Canada, for the class of work to be done. |
3 | Inspection of welds, including non-destructive test examination and verification of any required heat treatment process in accordance with rules or codes. |
4 | Verification of rotor balance and thermal stability testing in accordance with rules or codes. |
5 | Identification of components from component inspection certificates and inspection of components and their installation. |
6 | Witnessing of hydrostatic pressure tests of components in accordance with rules or codes. |
7 | Inspection of the constructed engine and witnessing of the engine operation under test. |
DIVISION IIInstallation Inspection
Item | Requirements |
---|---|
1 | Verification of correct alignment of securing arrangements. |
2 | Verification of correct adjustment and operational condition of the connection of the engine to associated systems. |
3 | Verification of correct adjustment and operational condition of safety, control and monitoring devices. |
4 | Verification of reliability and sufficiency under trials up to full power under normal working conditions for a suitable endurance period of not less than 2 hours, taking into consideration the size and the complexity of the gas turbine engine or steam turbine engine. |
PART IVPeriodic General and Special Inspections
DIVISION I(Section 19)Periodic General Inspection
Item | Requirements |
---|---|
1 | Operational condition of the engine. |
2 | Correct adjustment and operational condition of safety devices. |
3 | Locations where fluid leakage, metal wastage, overheating, heavy vibration or excessive bearing clearance may occur. |
4 | Correct adjustment of controls and monitoring systems. |
5 | Operational condition of alarm systems, particularly where the engine is designed for non-continuous local supervision. |
DIVISION IIPeriodic Special Inspection
SUBDIVISION I(Subsection 20(1))Parts to be Inspected
Item | Requirements |
---|---|
1 | Casings, glands, nozzles, blades, valves and valve mechanisms. |
2 | Rotors, blades, couplings, thrusts, bearings and bolts. |
3 | Speed-regulating governors and other safety devices. |
4 | Attached pumps. |
5 | Compressors, combustion chambers, heat exchangers, air inlet, fuel and exhaust, and starting system for a gas turbine engine. |
6 | Engine structure and fastenings without dismantling if a general examination shows that the condition of the components is adequate for further service. |
7 | No inspection is required for speed-regulating governors and other complex mechanisms where written information is provided to the inspector by firms specializing in the reconditioning of those mechanisms, indicating that the parts are in good order and adjustment. |
SUBDIVISION II(Subsection 20(2))Intervals
Item | Requirements |
---|---|
1 | For gas turbine engines and steam turbine engines, at intervals not exceeding 5 years. |
2 | Notwithstanding item 1, the first lifting of the casing and rotor of a steam turbine engine that has more than one propulsion ahead turbine with an emergency crossover arrangement is deferred until the engine is 10 years old if the inspector is satisfied that the turbine is in good operating condition based on the records of the vibration indicator, the rotor position indicator and the turbine operation. |
- SOR/2015-161, s. 7(F)
SCHEDULE VIReversing and Reduction Gearing, Shafting Systems and Propellers
PART I(Section 4)Design Specifications
DIVISION IReversing and Reduction Gearing
Item | Requirements |
---|---|
1 | None. |
DIVISION IIShafting Systems
Item | Requirements |
---|---|
1 | Screw shafts shall be made of
|
2 | The screw shaft shall have the propeller attached by means of
|
DIVISION IIIPropellers
Item | Requirements |
---|---|
1 | None. |
PART II(Section 6)Plans
DIVISION IReversing and Reduction Gearing
Item | Required Information |
---|---|
1 | General arrangement of the installation of the gearing in the ship, showing all connected systems. |
2 | General arrangement and sectional elevation of the gearing unit, including means of gearcase support. |
3 | Specifications indicating maximum input torque and corresponding revolutions per minute for each pinion, details of pinions and wheels, number of teeth, pitch, form and helix angles, details of wheel-rim attachment, gear-cutting and post-cutting processes, physical properties of principal parts, details of forgings, castings and weldments, details of the heat treatment process and testing procedures. |
4 | Details of gearcase, including access openings and venting arrangements. |
5 | Details of shafting systems, including couplings, clutches, reversing gear where fitted, and balancing and vibration analyses. |
6 | Details of bearings, lubricating oil systems and temperature monitoring devices. |
7 | Information set out in items 2 to 6 is not required to be submitted for a gearing system
|
DIVISION IIShafting Systems for Propulsion, Electrical Generators and Motors
Item | Required Information |
---|---|
1 | General arrangement of the propulsion shafting, the electrical generator shafting and motor shafting in the ship, showing all connected systems. |
2 | General arrangement and sectional elevation of the shafting systems, detailing attachments to driving and driven members and means of support. |
3 | Specifications indicating maximum input power and corresponding revolutions per minute, alignment of shafting system and bearing type and loading, physical properties of materials and testing procedures. |
4 | For ship propulsion shafting systems, details of
|
5 | Information set out in items 2 to 4 is not required to be submitted for shafting systems
|
DIVISION IIIFixed Pitch, Controllable Pitch and Directional Propellers
Item | Required Information |
---|---|
1 | General arrangement of the propeller, including details of fastening arrangement to the shafting systems. |
2 | Specifications indicating maximum input power and corresponding revolutions per minute, physical properties of materials, stress calculations and testing procedures. |
3 | Details of hub, hub mechanisms, seals, blade connections, control devices and locations. |
4 | Details of blade form and degree of controllability of pitch. |
5 | Information set out in items 2 to 4 is not required to be submitted for propellers not in excess of 225 kW continuous brake power. |
PART III(Subsection 12(2))Construction and Installation Inspections
DIVISION IConstruction Inspection
Item | Requirements |
---|---|
Reversing and Reduction Gearing | |
1 | Identification from material test certificates, before construction is commenced, of materials to be used, including welding metal, for the following parts:
|
2 | Verification that welding was carried out by welders certified by a Provincial Government of Canada, or another authority having similar standards where the welding was carried out outside Canada, for the class of work to be done. |
3 | Inspection of welds, including non-destructive test examination and verification of any required heat treatment process in accordance with rules or codes. |
4 | Verification of correct wheel-rim cutting, gear-cutting and post-cutting processes. |
5 | Verification of correct balance of rotating components. |
6 | Identification of components from component inspection certificates and inspection of components and their installation. |
7 | Inspection of the completed gearcase and witnessing of the gearing operation under test conditions. |
Shafting Systems for Propulsion, Electrical Generators and Motors | |
8 | Identification from material test or component inspection certificates, before construction is commenced, of materials to be used for the following parts:
|
9 | Inspection of the constructed components and confirmation of correct liner installation. |
Fixed Pitch, Controllable Pitch and Directional Propellers | |
10 | Identification from material test or component inspection certificates, before construction is commenced, of materials to be used for propellers, nuts, glands, keys, cones and, as applicable, hubs, blades, nuts, pitch and directional control mechanisms. |
11 | Inspection of assembled components, including non-destructive test examination as required by the inspector. |
DIVISION IIInstallation Inspection
Item | Requirements |
---|---|
1 | Verification of correct alignment of securing arrangements. |
2 | Verification of correct adjustment and operational condition the gearing, shafting systems, propellers and their connections to associated systems. |
3 | Verification of correct adjustment and operational condition of safety, control and monitoring devices. |
4 | Verification of reliability and sufficiency under trials up to full power capacity under normal working conditions for a suitable endurance period of not less than 2 hours, taking into consideration the size and complexity of the reversing and reduction gearing, shafting systems and propellers. |
PART IVPeriodic General Inspections and Periodic Special Inspections
DIVISION I(Section 19)Periodic General Inspection
Item | Requirements |
---|---|
Reversing and Reduction Gearing | |
1 | Operational condition of the gearing system. |
2 | Operational condition of the reversing system in reversing and reduction gearing. |
3 | Operational condition of the lubricating oil system. |
4 | Correct adjustment and operational condition of safety devices. |
5 | Locations where fluid leakage, overheating, heavy vibration or excessive gland or bearing clearances may occur. |
6 | Correct adjustment of controls and monitoring systems. |
7 | Operational condition of alarm systems, particularly where the reversing and reduction gearing is designed for non-continuous local supervision. |
Shafting Systems for Propulsion, Electrical Generators and Motors | |
8 | Operational condition of the lubricating fluid system. |
9 | Locations where overheating, vibration, fractures, excessive gland or bearing clearances may occur. |
10 | Screw shaft inspection, as far as practicable, without withdrawal, at the time of each dry-docking with the stern bearing wear-down being determined and recorded. |
Fixed Pitch, Controllable Pitch and Directional Propellers | |
11 | Operational condition of the propellers. |
12 | Correct adjustment of all controls and monitoring systems of controllable pitch and directional propellers. |
13 | Controllable pitch and directional propellers for any evidence of control fluid leakage. |
14 | Operational condition of all alarm systems for controllable pitch and directional propellers. |
DIVISION IIPeriodic Special Inspection
SUBDIVISION I(Subsection 20(1))Parts to be Inspected
Item | Requirements |
---|---|
Reversing and Reduction Gearing | |
1 | Subject to item 2, casing, pinions, wheels, shafts, couplings, clutches, glands, thrust bearing and selected other bearings, following removal of casing main cover. |
2 | Removal of casing main cover is not required if vibration or oil analysis, inspection through inspection doors and condition monitoring shows that the condition of the components is adequate for further service. |
3 | Gear-case ventilating system and safety devices. |
4 | Oil-flow indicating, filtering and temperature monitoring devices. |
Shafting Systems for Propulsion, Electrical Generators and Motors | |
5 | For intermediate shafts, thrust shafts, electrical generators and motor shafts
|
6 | For screw shafts,
|
Fixed Pitch, Controllable Pitch and Directional Propellers | |
7 | For fixed pitch propellers,
|
8 | For controllable pitch or directional propellers,
|
SUBDIVISION II(Subsection 20(2))Intervals
Item | Requirements |
---|---|
Reversing and Reduction Gearing | |
1 | At intervals not exceeding 5 years. |
Shafting Systems for Propulsion, Electrical Generators and Motors | |
2 | Intermediate shafts, thrust shafts, electrical generators and motor shafts, at intervals not exceeding 5 years. |
3 | Subject to items 4 to 7, screw shafts at intervals not exceeding 5 years. |
4 | Screw shafts in ships referred to in subsection 407(1) of the Act, at intervals not exceeding 4 years. |
5 | Screw shafts that meet the requirements of subitem 1(d) of Division II of Part I, at intervals not exceeding 2 years except for screw shafts in ships operating on voyages in fresh water only or between inland waters of Canada and not beyond Home Trade Class II limits where the ship operates in fresh water at least 3 months of the year, at intervals not exceeding 5 years. |
6 | For an oil-lubricated screw shaft having a keyless taper or flange for propeller attachment, a partial inspection without shaft withdrawal, at alternate periodic special inspections, if
|
7 | For a water-lubricated, corrosion-resistant metal screw shaft having a keyless taper or flange for propeller attachment, a partial inspection with limited shaft withdrawal, at alternate periodic special inspections, if
|
Fixed Pitch, Controllable Pitch and Directional Propellers | |
8 | Fixed pitch propellers, at the time of periodic special inspection of screw shafts. |
9 | Controllable pitch propellers
|
10 | Directional propellers, at intervals not exceeding 8 years if at the time of each dry docking the operation of the blades, bearing tolerances, bolting, sealing arrangements and operating or lubricating fluid analyses indicate that the directional propellers are suitable for further service. |
- SOR/2015-161, ss. 8(E), 9(F)
SCHEDULE VIISteering Systems, Shipside Components and Windlasses
PART I(Section 4)Design Specifications
DIVISION ISteering Systems
Item | Requirements |
---|---|
1 | A steering gear compartment shall
|
2 | All components and, in particular, non-duplicated essential components, shall be of sound and reliable construction, of adequate strength and protected against shock loading. |
3 | For essential components, bearings that are permanently lubricated or provided with lubrication fittings shall be utilized where required for the safe operation of the ship. |
4 | The pressure of the fluid for calculations to determine the scantlings of piping and steering gear components subjected to internal hydraulic pressure shall be at least 1.25 times the design working pressure under the operating conditions set out in item 9, taking into account any pressure that may exist in the low-pressure side of the system. |
5 | Where, due to dynamic loads on piping and steering gear components, pulsating pressures occur, the system design shall be such that fatigue does not cause material failure. |
6 | Relief valves shall be fitted to any part of the hydraulic system that can be isolated and in which pressure can be generated from the power source or from external forces. |
7 | Relief valve settings shall not exceed the design working pressure of the fluid set out in item 4 and the valves shall be of adequate size and arranged to avoid an undue rise in pressure above the design working pressure of the fluid. |
Steering Gears | |
8 | Subject to items 19 and 20, the installation shall consist of totally independent main and auxiliary steering gears. |
9 | The main steering gear shall be designed, where the ship is at its deepest sea-going draft and
|
10 | A main steering gear shall be power-operated
|
11 | The auxiliary steering gear shall be designed, where the ship is at its deepest sea-going draft and running ahead one-half its maximum service speed or 7 knots, whichever is the greater, to put the rudder over from 15 degrees on one side to 15 degrees on the other side in not more than 60 seconds. |
12 | The auxiliary steering gear shall have the capacity to be brought safely and rapidly into action in an emergency. |
13 | An auxiliary steering gear shall be power-operated
|
14 | A power-operated auxiliary steering gear unit and its associated control system and rudder angle indicator shall, where the rudder stock is required to be over 230 mm in diameter, excluding strengthening for navigation in ice, be provided automatically with an alternative power source within 45 seconds of the failure of the main power source, from
|
15 | The alternative power source referred to in item 14 shall
|
16 | Main and auxiliary steering gear power units shall be
|
17 | Hydraulic power-operated main and auxiliary steering gears shall be equipped with the following:
|
18 | Electric and electrohydraulic power-operated main and auxiliary steering gears shall meet the following requirements:
|
19 | An auxiliary steering gear is not required where main steering gear power units and connections are fitted in duplicate if
|
20 | An auxiliary steering gear is not required for double-ended ships with two independent steering systems, one fore and one aft, if in the case of failure of one of the steering systems the corresponding rudder can be safely and rapidly brought back to the centre line and kept steady in that position. |
21 | For every tanker, chemical tanker or gas carrier of 10,000 tons gross tonnage or more and every other ship of 70,000 tons gross tonnage or more, the main steering gear shall comprise two or more identical power units that meet the requirements of item 19. |
22 | Subject to item 23, every tanker, chemical tanker or gas carrier of 10,000 tons gross tonnage or more shall meet the following requirements:
|
23 | For tankers, chemical tankers or gas carriers of 10,000 tons gross tonnage or more, but of less than 100,000 tonnes deadweight, in the event of a single failure referred to in item 22 of a rudder actuator, the requirements set out in that item are not required to be met if
|
DIVISION IINon-Duplicated Rudder Actuators for Tankers, Chemical Tankers and Gas Carriers of 10,000 Tons Gross Tonnage or more but less than 100,000 Tonnes Deadweight
Item | Requirements |
---|---|
1 | Components that are subject to internal hydraulic pressure or that transmit mechanical forces to the rudder stock shall be made
|
2 | The design working pressure shall be at least equal to the greater of
|
3 | In determining the scantlings of components of rudder actuators subject to internal hydraulic pressure, the following stresses are permitted: Sm shall not exceed S1 shall not exceed Sb shall not exceed S1 + Sb shall not exceed Sm + Sb shall not exceed where
A and B are as follows: |
4 | Pressure-retaining components not requiring fatigue analysis and fracture mechanics analysis in accordance with subitem 7(d) of Division I of Part II are acceptable on the basis of a certified burst test and in that case, the detailed stress analysis required by subitem 7(c) of Division I of Part II is not required. |
5 | The minimum bursting pressure shall be calculated as follows: Pb = P. A sBa/SB where
|
6 | The construction shall minimize local concentrations of stress and all welded joints within the pressure boundary of a rudder actuator or connecting parts transmitting mechanical loads shall be of the full penetration type or of an equivalent strength. |
7 | Oil seals between non-moving components, forming part of the external pressure boundary, shall be of the metal-on-metal type or of an equivalent type. |
8 | Oil seals between moving components, forming part of the external pressure boundary, shall be duplicated, so that the failure of one seal does not render the actuator inoperative, or shall have sealing arrangements providing equivalent protection against leakage. |
9 | Isolating valves shall be fitted at the connection of pipes to the actuator and shall be directly mounted on the actuator. |
10 | Relief valves for protecting the rudder actuator against over-pressure as required by items 6 and 7 of Division I shall meet the following requirements:
|
11 | The rudder actuator shall be subjected to non-destructive testing in accordance with rules or codes to detect both surface flaws and volumetric flaws, and fracture mechanics analysis may be used for determining maximum allowable flaw size. |
DIVISION IIISteering Controls
Item | Requirements |
---|---|
1 | Steering-wheels or lever pointers shall
|
2 | A rudder direction and angle indicator, independent of the remote steering gear control system, shall be fitted on the bridge where the main steering system is power-operated or the length of the ship exceeds 20 m. |
3 | Main steering gears shall be controllable from the bridge and from an alternative location in the steering gear compartment or other suitable location taking into account operational and risk factors. |
4 | A rudder angle indicator shall be fitted at the alternative location referred to in item 3. |
5 | Subject to item 6, two independent remote control systems, not including the steering-wheel or lever, shall be fitted where a duplicate main steering gear system is fitted. |
6 | Except in a tanker, chemical tanker or gas carrier of 10,000 tons gross tonnage or more a second independent control system is not required to be fitted where the control system is a hydraulic telemotor. |
7 | The auxiliary steering gear shall be controllable from the steering gear compartment and, if power-operated, shall be operable from the bridge and independent of the main steering gear control system. |
8 | Any main and auxiliary steering gear control system operable from the bridge shall meet the following requirements:
|
9 | Duplicate steering gear control systems, including pipes, electric power circuits and their components shall be separated, as far as practicable, throughout their length. |
DIVISION IVShipside Components
Item | Requirements |
---|---|
1 | For ships required to operate in ice-covered waters where ice may choke sea-water inlets, maintenance of essential sea-water supply shall be maintained by
|
DIVISION VWindlasses
Item | Requirements |
---|---|
1 | None. |
PART II(Section 6)Plans
DIVISION ISteering Systems
Item | Required Information |
---|---|
1 | General arrangement of the main, and duplicate or auxiliary, steering systems in the ship. |
2 | General arrangement and sectional elevation of the steering gears, including holding-down arrangements. |
3 | Specifications indicating maximum designed torque at rudder stock, timing and angle of rudder movements for main and auxiliary steering gears, materials and physical properties of the principal components. |
4 | Details of pumps, piping and valves subjected to pressure, and securing arrangements. |
5 | Details of safety and shock-prevention devices. |
6 | Details of control and monitoring mechanisms including connections to all steering locations. |
7 | For non-duplicated rudder actuators in tankers, chemical tankers and gas carriers of 10,000 tons gross tonnage or more but less than 100,000 tonnes deadweight,
|
8 | Information for valves and similar minor components referred to in item 4 is not required to be submitted where a manufacturer or an approved classification society certifies that the types of valves or similar minor components have been designed and constructed in accordance with rules or codes. |
9 | Information for pumps referred to in item 4 is not required to be submitted where an approved classification society certifies that the pumps have been designed and constructed in accordance with rules or codes, except that the driving motor or engines of the pumps shall meet the requirements of Part II of the applicable schedule of Schedules I to XV. |
DIVISION IIShipside Components
Item | Required Information |
---|---|
Shafting and Valves | |
1 | Details of shipside penetrating shafting and glands, including fin stabilizing components, their locking mechanisms and other connections. |
2 | Details of sea inlet and discharge valves and strainers and their connections, including those for side thrusters and deck wash systems. |
3 | For ships required to operate in ice-covered waters, details of arrangements to prevent slush ice choking sea-water inlets. |
4 | Specifications indicating the maximum stresses of the shafting, valve pressures and flow rates, materials and physical properties of the principal components. |
Door-operating Mechanisms | |
5 | General arrangement of door-operating mechanisms showing all connected machinery and their locations in the ship. |
6 | Details of all components, including pumps, piping and valves subjected to pressure and securing arrangements. |
7 | Specifications indicating maximum stresses, materials and physical properties of principal components, particularly those that may be subjected to low ambient temperatures. |
8 | Information for valves and similar minor components referred to in items 2 and 6 is not required to be submitted where a manufacturer or an approved classification society certifies that the types of valves or similar minor components have been designed and constructed in accordance with rules or codes. |
9 | Information for pumps referred to in item 6 is not required to be submitted where an approved classification society certifies that the pumps have been designed and constructed in accordance with rules or codes, except that the driving motor or engines of the pumps shall meet the requirements of Part II of the applicable schedule of Schedules I to XV. |
DIVISION IIIWindlasses
Item | Required Information |
---|---|
1 | General arrangement, including type of power and loads, of the windlass systems showing all connected machinery and their location in the ship. |
2 | Details of all windlass components, including pumps, piping, valves and brakes, and securing arrangements. |
3 | Specifications indicating maximum stresses, materials and physical properties of principal components, particularly those which may be subjected to low ambient temperatures. |
4 | Information for windlasses referred to in items 2 and 3 is not required to be submitted where an approved classification society certifies that the windlasses have been designed and constructed in accordance with rules or codes except that the driving motor or engines of the pumps shall meet the requirements of Part II of the applicable schedule of Schedules I to XV. |
PART III(Subsection 12(2))Construction and Installation Inspections
DIVISION IConstruction Inspection
Item | Requirements |
---|---|
Steering Systems | |
1 | Identification from material test certificates, before construction is commenced, of materials to be used, including welding metal, for the following parts:
|
2 | Verification that welding was carried out by welders certified by a Provincial Government of Canada, or another authority having similar standards where the welding was carried out outside Canada, for the class of work to be done. |
3 | Inspection of welds, including non-destructive test examination and verification of the heat treatment process, in accordance with rules or codes. |
4 | Identification of components from component inspection certificates and inspection of components and their installation. |
5 | Witnessing of hydrostatic pressure testing of components in accordance with rules or codes, except that for non-duplicated rudder actuator pressure components in tankers, chemical tankers and gas carriers of 10,000 tons gross tonnage or more but less than 100,000 tonnes deadweight, the hydrostatic pressure test is to be at 1.5 times the design working pressure. |
6 | Inspection of the constructed steering gear and the witnessing of the gearing operation under test. |
Shipside Components and Windlasses | |
7 | None. |
DIVISION IIInstallation Inspection
Item | Requirements |
---|---|
Steering Systems | |
1 | Identification from component inspection certificates, before installation is commenced, of steering systems. |
2 | Verification of correct adjustment and operational condition at all steering locations of securing arrangements, connection of steering systems to associated systems, safety, control and monitoring devices and, for hydraulic power operated systems, a hydrostatic pressure test at the design working pressure. |
3 | Inspection of change-over from main to duplicate or auxiliary steering systems in accordance with the design specifications set out in Part I. |
4 | Verification of reliability and sufficiency of both main, and duplicate or auxiliary steering systems under trials for a sufficient endurance period up to the ship’s maximum propulsion power for main and duplicate systems and up to navigable speed for the auxiliary system in accordance with design specifications set out in Division I of Part I, except that the steering gear need not necessarily be demonstrated at maximum rudder angle operation while running astern at maximum speed. |
Shipside Components and Windlasses | |
5 | Identification from component inspection certificates, before installation is commenced, of shipside components, including door-operating mechanisms, and windlasses. |
6 | Verification of correct adjustment and operational condition of securing arrangements, connection of the components and windlasses to associated systems, safety, control and monitoring devices. |
7 | Inspection of shafts, glands, strainers and valves. |
8 | Inspection to ensure that no overboard discharges are in the way of lifeboat or liferaft lowering locations. |
9 | Witnessing of operational tests of the components and windlasses in accordance with rules or codes. |
PART IVPeriodic General Inspections and Periodic Special Inspections
DIVISION I(Section 19)Periodic General Inspection
Item | Requirements |
---|---|
Steering Systems | |
1 | Operational condition and controllability of steering systems from all steering locations. |
2 | Capability of duplicate or auxiliary steering systems to be brought rapidly into operation. |
3 | Correct adjustment and operational condition of alarm and monitoring devices. |
4 | Correct adjustment and operational condition of safety devices. |
5 | Locations where fluid leakage, overheating, excessive vibration, fractures or excessive gland or bearing clearances may occur, particularly where the steering gear includes only a single rudder actuator. |
Shipside Components and Windlasses | |
6 | Operational conditional and controllability of components including door-operating mechanisms and windlass braking systems. |
7 | Locations where excessive fluid leakage, metal wastage, vibration or fractures may occur. |
8 | Overboard discharges to confirm that no overboard discharges above the ship waterline are in the way of lifeboat or liferaft lowering positions. |
DIVISION IIPeriodic Special Inspection
SUBDIVISION I(Subsection 20(1))Parts to be Inspected
Item | Requirements |
---|---|
Steering Systems | |
1 | Subject to item 4, driving engines or pumps, actuators, piping, pintles and bearings. |
2 | Subject to item 4, control and monitoring mechanisms leading to the bridge and other steering locations. |
3 | Steering gear structure and fastenings without dismantling, if their condition is adequate on the basis of general examination. |
4 | Periodic special inspection is not required for hydraulic systems if the general periodic inspection referred to in Division I and operational observation, vibration analysis or written information provided to the inspector by firms specializing in the reconditioning of these parts shows that the condition of the parts is satisfactory for further service. |
5 | No periodic special inspection is required for complex mechanisms where written information is provided to the inspector by firms specializing in the reconditioning of these parts, indicating that the parts are in good order and adjustment. |
Shipside Components and Windlasses | |
6 | Internal and external parts of shipside valves, keel cooler valves, strainers and glands. |
7 | Periodic special inspection is not required for hydraulic pumps, cylinders, rams, piping and windlasses if the periodic general inspection referred to in Division I and operational observation, vibration analysis or written information provided to the inspector by firms specializing in the reconditioning of these parts shows that the condition of the parts is satisfactory for further service. |
8 | No periodic special inspection is required for complex mechanisms where written information is provided to the inspector by firms specializing in the reconditioning of these parts, indicating that the parts are in good order and adjustment. |
SUBDIVISION II(Subsection 20(2))Intervals
Item | Requirements |
---|---|
Steering Systems | |
1 | At intervals not exceeding 5 years. |
Shipside Components | |
2 | Shipside valves, keel cooler valves, strainers, shafts and glands, at intervals not exceeding 4 years except where the ship is dry docked at intervals of 5 years in accordance with the Hull Inspection Regulations, at that time. |
3 | All other components including door-operating mechanisms, at intervals not exceeding 5 years. |
- SOR/2015-161, ss. 10(E), 11, 12(E), 13(E), 14(F), 15(E), 16(E)
SCHEDULE VIIIRemote Control and Monitoring Systems in Periodically Unattended Machinery Spaces
PART I(Section 4)Design Specifications
DIVISION IApplication
Item | Description of Ships |
---|---|
1 | In this schedule, Group 1 ship means a ship in which machinery is controlled and monitored from the bridge and engineers do not maintain surveillance watch duties in the machinery spaces and that is certificated for the following voyages:
Group 2 ship means a ship in which machinery may be controlled from the bridge and at least one engineer is on watch in a remote central control room location only and that is certificated for the following voyages:
Group 3 ship means a ship
|
2 | This Schedule does not apply to Group 1, 2 or 3 ships that are
|
DIVISION IIGroup 1, 2 and 3 Ships
Item | Requirements |
---|---|
1 | Remote and automatic control and monitoring of machinery located in periodically unattended spaces shall offer the same level of safety from remote control locations as would be obtained if the machinery were arranged for continuous local manual control and monitoring by watchkeeping engineers. |
2 | Control, monitoring and safety devices and their location shall meet the requirements set out in rules or codes in respect of ship motion, structural vibration and atmospheric environment. |
3 | Every enclosed central control location shall have two means of access located remote from each other, except where such enclosures are so small that two means of access are impracticable. |
4 | Two sources of power to ensure continuous operation shall be provided for control, monitoring and alarm systems, and
|
5 | Failure of control, monitoring and alarm systems or their power supply shall activate an audible and visual alarm at the central control location. |
6 | An audible and visual alarm system shall be provided to indicate any fault requiring attention and shall
|
7 | The alarm system shall be equipped to indicate at the same time more than one fault and the acceptance of an alarm shall not inhibit another alarm. |
8 | Acceptance at either of the locations referred to in subitem 6(a) of an alarm shall be indicated at the location where the alarm was activated. |
9 | An audible alarm shall sound until it is accepted and the visual indication of the alarm shall remain until the fault has been corrected, after which the alarm system shall automatically reset to the normal operating condition. |
10 | Machinery controls shall be designed to remain accurate throughout the operating range and to have fail safe characteristics. |
11 | Machinery controls shall be robust and easy to operate, not cause undue stress in systems being controlled and operate in a logical direction and sequence with a detent at the stop or neutral position. |
12 | A safety system shall be provided to ensure that a serious malfunction in boiler and other machinery operations that presents an immediate danger initiates the automatic shut-down of the boiler or other machinery and activates an alarm, except that shut-down of the propulsion system shall only be automatically activated in cases that could lead to serious damage, complete breakdown or explosion. |
13 | Where arrangements for overriding the shut-down of the main propelling machinery are fitted, the arrangements shall be such as to preclude inadvertent operation, and visual means shall be provided to indicate when the override has been activated. |
14 | Remote-controlled machinery systems and periodically unattended machinery spaces shall be equipped as follows:
|
15 | A reliable means of voice communication shall be provided between the main machinery control location or propulsion machinery control location and the bridge, the engineers’ cabins and the engineers’ public rooms. |
16 | Propulsion machinery orders from the bridge shall be indicated in the main machinery control room or at the propulsion machinery control station. |
17 | Manuals for the proper operation and maintenance of remote control and monitoring systems, containing all necessary information for normal and emergency operation and maintenance shall be provided aboard ship. |
18 | Testing procedure manuals for remote control and monitoring systems shall be provided aboard ship and the testing procedures shall
|
DIVISION IIIGroup 1 and 2 Ships
Item | Requirements | |
---|---|---|
Machinery | ||
1 | Internal combustion engines of 2250 kW or more or having cylinders of more than 300 mm bore shall be provided with crankcase oil mist detectors, engine-bearing temperature monitors or equivalent devices. | |
2 | Where internal combustion engines are used for main propulsion, means shall be provided to keep the starting air pressure at the level required to start the engine. | |
3 | The number of consecutive automatic attempts that fail to start an engine shall be limited in order to safeguard sufficient starting air pressure and an audible alarm set at a level that permits starting of the propulsion machinery shall be provided to indicate low starting air pressure. | |
4 | The main source of electrical power shall meet the following requirements:
| |
5 | Where electrical power is supplied simultaneously by more than one generator in parallel operation, provision shall be made in case of failure of one of the operating generator sets to keep the remaining generator sets in operation without overload to permit propulsion and steering, and to ensure the safety of the ship. | |
6 | Where stand-by machines are necessary for the operation of other auxiliary machinery essential to propulsion, automatic change-over devices shall be fitted. | |
Controls and Alarms | ||
7 | Under all operating conditions the speed, direction of thrust and, where applicable, the pitch of the propeller shall be fully controllable by remote control from the bridge. | |
8 | The remote control shall be operated by a single control device for each independent propeller with automatic performance of all associated services without causing overload of the propulsion machinery. | |
9 | The main propulsion machinery shall be equipped with an emergency stopping device on the bridge that is independent of the bridge control system. | |
10 | The control system shall be such that the services needed for the operation of the main propulsion machinery and its auxiliaries are performed automatically. | |
11 | An audible and visual alarm shall be activated when the automatic change-over of the control power source is activated. | |
12 | An alarm system that meets the requirements of items 7 to 9 of Division II shall be provided for all pressures, temperatures, fluid levels and other data essential to the safe operation of the ship. | |
13 | A centralized control location shall be arranged with the necessary alarm panels and instrumentation to indicate that an alarm has been activated. | |
14 | Remote control of the propulsion machinery shall be possible only from one location at a time and inter-connected control positions are permitted at each location. | |
15 | At each location there shall be an indicator showing which location is in control of the propulsion machinery and the transfer of control between the bridge and machinery spaces shall be possible only in the main machinery space or in the machinery control room. | |
16 | The control system shall include means to prevent, when the system transfers control from one location to another, the propelling thrust from altering to the extent that control of the ship is endangered. | |
17 | All machinery essential for the safe operation of the ship shall be capable of being controlled locally. | |
18 | The design of the remote automatic control system shall be such that an alarm is given on failure of the system and, unless impracticable, the preset speed and direction of thrust of the propeller is maintained until local control is in operation. | |
19 | Indicators shall be fitted on the bridge for
| |
20 | Bilge wells in periodically unattended machinery spaces shall be located and monitored in such a way that the accumulation of liquids is detected at normal angles of trim and heel, and shall be large enough to easily accommodate normal drainage during an unattended period. | |
21 | Where the bilge pumps are capable of being started automatically, visual and audible alarms shall be provided to indicate when the influx of liquid is greater than the pump capacity or when the pump is operating more frequently than would be expected under normal conditions. | |
22 | Where automatic bilge pumps are fitted,
| |
23 | The position of the controls of any valve serving a sea inlet, a discharge below the water-line or a bilge injection system shall be located to allow adequate time for operation of the controls in case of an influx of water to the space, having regard to the time likely to be required to reach and operate the controls. | |
24 | Arrangements shall be made to operate the controls from a position above the level to which the unattended space might become flooded when the ship is fully loaded. |
DIVISION IVGroup 3 Ships
SUBDIVISION I
Item | Application |
---|---|
1 | In this Division, the bridge control station includes the wheelhouse, its top and wings. |
SUBDIVISION II
Item | Requirements | |||||||||||||||||||||||||||||||||||||||||||||||||||||||||||||||||||||||||||||||||||||||||||||||||
---|---|---|---|---|---|---|---|---|---|---|---|---|---|---|---|---|---|---|---|---|---|---|---|---|---|---|---|---|---|---|---|---|---|---|---|---|---|---|---|---|---|---|---|---|---|---|---|---|---|---|---|---|---|---|---|---|---|---|---|---|---|---|---|---|---|---|---|---|---|---|---|---|---|---|---|---|---|---|---|---|---|---|---|---|---|---|---|---|---|---|---|---|---|---|---|---|---|---|
Main and Auxiliary Machinery Controls | ||||||||||||||||||||||||||||||||||||||||||||||||||||||||||||||||||||||||||||||||||||||||||||||||||
1 | Control locations shall have a visual indicator to show when they are in command and the central control location shall have monitors and alarms in accordance with items 65 and 66. | |||||||||||||||||||||||||||||||||||||||||||||||||||||||||||||||||||||||||||||||||||||||||||||||||
2 | The machinery control arrangement shall be such that only one location can be in control at any one time, and with the exception of the override capability referred to in item 8, transfer of control from the central control location to local control shall not be possible until the receiving location has indicated its readiness to accept the intended transfer. | |||||||||||||||||||||||||||||||||||||||||||||||||||||||||||||||||||||||||||||||||||||||||||||||||
3 | All essential machinery shall be capable of being fully operated locally when remote or automatic control systems are not operating. | |||||||||||||||||||||||||||||||||||||||||||||||||||||||||||||||||||||||||||||||||||||||||||||||||
4 | Transfer to local control of machinery shall be easily and rapidly accomplished and any material or tools required to effect the transfer shall be permanently located at a convenient location adjacent to the machinery. | |||||||||||||||||||||||||||||||||||||||||||||||||||||||||||||||||||||||||||||||||||||||||||||||||
5 | Where an engine is arranged to start automatically or by remote control, interlocks shall be provided to prevent starting of the engine under conditions that could be hazardous to the machinery, which conditions shall include turning gear engaged, low lubricating-oil pressure and, where applicable, shaft brake engaged. | |||||||||||||||||||||||||||||||||||||||||||||||||||||||||||||||||||||||||||||||||||||||||||||||||
6 | Where an internal combustion engine is arranged to start automatically, the number of consecutive automatic attempts to start the engine without success shall be limited in order to safeguard sufficient starting air pressure or in the case of electric starting, sufficient battery power, for local attempts to start the engine. | |||||||||||||||||||||||||||||||||||||||||||||||||||||||||||||||||||||||||||||||||||||||||||||||||
Main Propulsion Systems | ||||||||||||||||||||||||||||||||||||||||||||||||||||||||||||||||||||||||||||||||||||||||||||||||||
7 | Means shall be provided at the central control location and locally at the engines themselves to stop the main propulsion engines in an emergency and the emergency stopping devices shall be independent of the normal control system and adequately protected against accidental damage or operation. | |||||||||||||||||||||||||||||||||||||||||||||||||||||||||||||||||||||||||||||||||||||||||||||||||
8 | Local control of the main propulsion engines shall have capability of overriding the remote control systems and there shall be an audible and visual alarm to alert the locations affected by an override in accordance with subitem 65(a)(i). | |||||||||||||||||||||||||||||||||||||||||||||||||||||||||||||||||||||||||||||||||||||||||||||||||
9 | For ships of not more than 150 tons gross tonnage remote propulsion engine controls are not required to be power-operated and are not required to be in duplicate. | |||||||||||||||||||||||||||||||||||||||||||||||||||||||||||||||||||||||||||||||||||||||||||||||||
10 | Prolonged running of a main propulsion engine in a restricted speed range shall be prevented automatically or an indication of restricted speed ranges shall be posted at each control location. | |||||||||||||||||||||||||||||||||||||||||||||||||||||||||||||||||||||||||||||||||||||||||||||||||
Steering Systems | ||||||||||||||||||||||||||||||||||||||||||||||||||||||||||||||||||||||||||||||||||||||||||||||||||
11 | In the event of failure of the main steering system there shall be an auxiliary system capable of being brought into operation from the central control location within 45 seconds. | |||||||||||||||||||||||||||||||||||||||||||||||||||||||||||||||||||||||||||||||||||||||||||||||||
Electrical Power Systems | ||||||||||||||||||||||||||||||||||||||||||||||||||||||||||||||||||||||||||||||||||||||||||||||||||
12 | In the event of failure of the electrical generator supplying ship service power where generated electrical energy is required for essential service, there shall be a stand-by generator capable of assuming all essential electrical load and, for ships in excess of 150 tons gross tonnage, the stand-by generator shall be arranged to assume the load automatically within 45 seconds. | |||||||||||||||||||||||||||||||||||||||||||||||||||||||||||||||||||||||||||||||||||||||||||||||||
Boilers and Hot-Air Heating Units | ||||||||||||||||||||||||||||||||||||||||||||||||||||||||||||||||||||||||||||||||||||||||||||||||||
13 | Steam and hot-water boilers, hot-air heating units and associated systems shall be capable of automatic operation and of meeting requirements within design limitations under all working conditions. | |||||||||||||||||||||||||||||||||||||||||||||||||||||||||||||||||||||||||||||||||||||||||||||||||
14 | Automatic operation shall include, as applicable, controls and monitors for fuel flow and temperature, combustion air flow, burner flame, feed-water flow, feed-water contamination by salt or oil, boiler pressure and hot-air heating unit circulating air flow. | |||||||||||||||||||||||||||||||||||||||||||||||||||||||||||||||||||||||||||||||||||||||||||||||||
15 | The control and monitoring equipment shall be designed to prevent unsafe operation of the boiler or hot-air heating unit. | |||||||||||||||||||||||||||||||||||||||||||||||||||||||||||||||||||||||||||||||||||||||||||||||||
16 | Any failure of control and monitoring equipment shall prevent continued operation of the boiler or hot-air heating unit and cause the fuel supply to be cut off and an audible and visual alarm to be activated in accordance with subitem 65(e). | |||||||||||||||||||||||||||||||||||||||||||||||||||||||||||||||||||||||||||||||||||||||||||||||||
17 | A master fuel oil shut-off valve shall be fitted in the fuel supply line and shall close automatically in the event of
| |||||||||||||||||||||||||||||||||||||||||||||||||||||||||||||||||||||||||||||||||||||||||||||||||
18 | A fuel oil shut-off valve shall be fitted to each burner in the fuel supply line and the valve shall close automatically in the case of flame failure or whenever the automatic program requires that the master fuel oil shut-off valve be closed. | |||||||||||||||||||||||||||||||||||||||||||||||||||||||||||||||||||||||||||||||||||||||||||||||||
19 | Automatic combustion controls shall be fitted to provide an adequate fuel-to-air ratio throughout the operational range. | |||||||||||||||||||||||||||||||||||||||||||||||||||||||||||||||||||||||||||||||||||||||||||||||||
20 | Where the system is designed to light the initial burner automatically or from a remote location, purging of the combustion chamber and convection spaces shall automatically take place for a period that is sufficient to ensure at least four changes of air, which period shall last at least 15 seconds. | |||||||||||||||||||||||||||||||||||||||||||||||||||||||||||||||||||||||||||||||||||||||||||||||||
21 | Adequate air flow and the correct position of the air registers and dampers shall be indicated before the purging period starts. | |||||||||||||||||||||||||||||||||||||||||||||||||||||||||||||||||||||||||||||||||||||||||||||||||
22 | Fuel oil may be ignited by an electrical spark generated by a transformer having an output of not less than 10,000 volts, a glow plug or a light-oil pilot flame that has been electrically ignited. | |||||||||||||||||||||||||||||||||||||||||||||||||||||||||||||||||||||||||||||||||||||||||||||||||
23 | A means of ignition system described in item 22 shall be provided for burners that are automatically or remote controlled. | |||||||||||||||||||||||||||||||||||||||||||||||||||||||||||||||||||||||||||||||||||||||||||||||||
24 | The electrical ignition system shall be energized before or simultaneously with the introduction of fuel or light oil and shall remain energized during the trial-for-ignition period referred to in item 25. | |||||||||||||||||||||||||||||||||||||||||||||||||||||||||||||||||||||||||||||||||||||||||||||||||
25 | Where fuel or light oil is electrically ignited, the flame safeguard control system shall provide a trial-for-ignition period of not more than 15 seconds, during which fuel or light oil may be introduced to the ignition source and, if a flame is not established within 15 seconds, the oil supply valve shall close automatically. | |||||||||||||||||||||||||||||||||||||||||||||||||||||||||||||||||||||||||||||||||||||||||||||||||
26 | Where fuel oil is ignited by a light-oil pilot flame, the flame safeguard control shall provide a trial-for-ignition period of not more than 15 seconds, during which fuel oil may be introduced to the pilot flame and if a fuel oil flame is not established within 15 seconds the fuel oil supply valve to the pilot flame shall close automatically. | |||||||||||||||||||||||||||||||||||||||||||||||||||||||||||||||||||||||||||||||||||||||||||||||||
27 | Fuel oil shall not be supplied to a burner before the light-oil pilot flame has been confirmed. | |||||||||||||||||||||||||||||||||||||||||||||||||||||||||||||||||||||||||||||||||||||||||||||||||
28 | Flame safeguard controls of the thermostatic type operated by means of an open bi-metallic helix shall not be used. | |||||||||||||||||||||||||||||||||||||||||||||||||||||||||||||||||||||||||||||||||||||||||||||||||
29 | A flame safeguard control shall be provided to each burner so that the fuel oil supply valve can be closed in not more than four seconds in the event of flame failure and the master fuel oil shut-off valve can be closed in the event of flame failure at all burners. | |||||||||||||||||||||||||||||||||||||||||||||||||||||||||||||||||||||||||||||||||||||||||||||||||
30 | The failure of a component in the flame safeguard control shall cause a shut-down of the burner and the design of the control shall prevent automatic restarting. | |||||||||||||||||||||||||||||||||||||||||||||||||||||||||||||||||||||||||||||||||||||||||||||||||
31 | The flame safeguard control shall be fitted with an audible and visual alarm in the event of flame failure and the control shall require resetting for restart purposes. | |||||||||||||||||||||||||||||||||||||||||||||||||||||||||||||||||||||||||||||||||||||||||||||||||
32 | A low-fire interlock shall be fitted to a multi-burner boiler so that the lowest burner is ignited first, and the other burners shall not be ignited until the scanner indicates that there is a flame in the lowest burner. | |||||||||||||||||||||||||||||||||||||||||||||||||||||||||||||||||||||||||||||||||||||||||||||||||
Steam Boilers | ||||||||||||||||||||||||||||||||||||||||||||||||||||||||||||||||||||||||||||||||||||||||||||||||||
33 | Automatically operated steam boilers shall be fitted with water-level controls and low water-level limit controls. | |||||||||||||||||||||||||||||||||||||||||||||||||||||||||||||||||||||||||||||||||||||||||||||||||
34 | Water-level controls and low water-level limit controls may be of the float, electrode probe, thermostatic expansion tube or thermo-hydraulic type. | |||||||||||||||||||||||||||||||||||||||||||||||||||||||||||||||||||||||||||||||||||||||||||||||||
35 | Water-level controls and low water-level limit controls shall be located to minimize the effect of the roll and pitch of the ship. | |||||||||||||||||||||||||||||||||||||||||||||||||||||||||||||||||||||||||||||||||||||||||||||||||
36 | The low water-level limit control shall close the master fuel oil shut-off valve when the water level falls to a minimum safe level visible in the gauge glass and the system may include a five-second time delay to avoid shut-down due to the rolling and pitching of the ship. | |||||||||||||||||||||||||||||||||||||||||||||||||||||||||||||||||||||||||||||||||||||||||||||||||
37 | After operation of the low water-level limit control, manual resetting of the control shall be required before the boiler burners can be re-lit. | |||||||||||||||||||||||||||||||||||||||||||||||||||||||||||||||||||||||||||||||||||||||||||||||||
38 | Float-operated water-level and low water-level limit controls shall be so constructed that they will not be damaged by water levels above or below the operating range. | |||||||||||||||||||||||||||||||||||||||||||||||||||||||||||||||||||||||||||||||||||||||||||||||||
39 | The low water-level limit control shall have independent connections to the boiler. | |||||||||||||||||||||||||||||||||||||||||||||||||||||||||||||||||||||||||||||||||||||||||||||||||
40 | Water-level controls shall be so constructed that the water inlet valve cannot feed water into the boiler through the float chamber. | |||||||||||||||||||||||||||||||||||||||||||||||||||||||||||||||||||||||||||||||||||||||||||||||||
41 | No outlet connection shall be placed on
| |||||||||||||||||||||||||||||||||||||||||||||||||||||||||||||||||||||||||||||||||||||||||||||||||
42 | For controls that are external to the boiler drum, the connections shall be fitted with shut-off valves locked and sealed in the open position and attached directly to the boiler drum. | |||||||||||||||||||||||||||||||||||||||||||||||||||||||||||||||||||||||||||||||||||||||||||||||||
Auxiliary Systems | ||||||||||||||||||||||||||||||||||||||||||||||||||||||||||||||||||||||||||||||||||||||||||||||||||
43 | Subject to item 44, pumps and other components essential for main propulsion engine operation shall have stand-by pumps and components, and for ships of more than 150 tons gross tonnage, the stand-by pumps and components shall be arranged to start up automatically on failure of the operating pumps or other components. | |||||||||||||||||||||||||||||||||||||||||||||||||||||||||||||||||||||||||||||||||||||||||||||||||
44 | In multi-engined ships where engines have integral pumps, a spare pump readily available for installation may be used in lieu of an automatic-starting stand-by pump. | |||||||||||||||||||||||||||||||||||||||||||||||||||||||||||||||||||||||||||||||||||||||||||||||||
45 | Air compressors, refrigeration systems and other ship service systems that are essentially independent and self-controlled need not be controlled from a remote control location. | |||||||||||||||||||||||||||||||||||||||||||||||||||||||||||||||||||||||||||||||||||||||||||||||||
46 | Bilge water high-level audible and visual alarms shall be fitted at the central control location in accordance with subitem 65(f)(vi) and shall monitor the following bilges:
| |||||||||||||||||||||||||||||||||||||||||||||||||||||||||||||||||||||||||||||||||||||||||||||||||
47 | The bilge pumping systems shall be arranged to function for a reasonable period after the sounding of the bilge high-level alarm taking into account the size of the space bilges. | |||||||||||||||||||||||||||||||||||||||||||||||||||||||||||||||||||||||||||||||||||||||||||||||||
48 | Where automatic bilge pumps are fitted
| |||||||||||||||||||||||||||||||||||||||||||||||||||||||||||||||||||||||||||||||||||||||||||||||||
49 | Subject to item 50, the fire control system shall incorporate at least one fire pump capable of being controlled from the fire control location set out in subitem 14(e) of Division II. | |||||||||||||||||||||||||||||||||||||||||||||||||||||||||||||||||||||||||||||||||||||||||||||||||
50 | For ships of 150 tons gross tonnage or less a manual fire pump and its controls, including means of opening the sea valve, may be installed in a suitable location on the deck in lieu of a remote-controlled pump. | |||||||||||||||||||||||||||||||||||||||||||||||||||||||||||||||||||||||||||||||||||||||||||||||||
51 | Where valves in essential systems are normally closed to prevent frost damage to exposed piping, the controls for the valves shall be in readily accessible locations. | |||||||||||||||||||||||||||||||||||||||||||||||||||||||||||||||||||||||||||||||||||||||||||||||||
52 | Where remote controls for valves are fitted, valve status indicators shall be fitted at the locations for the valve controls and valves located in locations liable to be flooded shall be capable of operating when submerged. | |||||||||||||||||||||||||||||||||||||||||||||||||||||||||||||||||||||||||||||||||||||||||||||||||
53 | Where machinery space watertight doors are fitted, controls shall be fitted in accordance with the Hull Construction Regulations. | |||||||||||||||||||||||||||||||||||||||||||||||||||||||||||||||||||||||||||||||||||||||||||||||||
54 | Fuel oil service tanks shall be capable of holding sufficient fuel for the total period of the normal ship operational route or for 24 hours normal operation, whichever is the lesser, at full power, except that where provision is made for automatic filling, the period may be reduced to eight hours. | |||||||||||||||||||||||||||||||||||||||||||||||||||||||||||||||||||||||||||||||||||||||||||||||||
55 | If fuel tanks are required to be heated, fuel oil temperature shall be monitored and thermostatically controlled or the fuel tanks shall be fitted with a high-temperature audible and visual alarm in accordance with subitem 65(f)(iii). | |||||||||||||||||||||||||||||||||||||||||||||||||||||||||||||||||||||||||||||||||||||||||||||||||
Remote Monitors | ||||||||||||||||||||||||||||||||||||||||||||||||||||||||||||||||||||||||||||||||||||||||||||||||||
56 | The central control location shall include monitoring indicators as set out in items 65 and 66. | |||||||||||||||||||||||||||||||||||||||||||||||||||||||||||||||||||||||||||||||||||||||||||||||||
57 | Where continuously reading indicators are impracticable, demand display types may be fitted. | |||||||||||||||||||||||||||||||||||||||||||||||||||||||||||||||||||||||||||||||||||||||||||||||||
58 | Direct reading indicators shall be fitted at the location of the machinery. | |||||||||||||||||||||||||||||||||||||||||||||||||||||||||||||||||||||||||||||||||||||||||||||||||
59 | Where the control system automatically shuts down machinery for any reason, regaining of control following correction of the fault shall not be possible without reset action and without bringing the control to the stop position. | |||||||||||||||||||||||||||||||||||||||||||||||||||||||||||||||||||||||||||||||||||||||||||||||||
60 | Alarms associated with machinery control and safety shall be clearly distinguishable from fire-alarms and, where possible, the arrangements of the alarms shall be such that the alarm is activated before failure and shut-down occurs. | |||||||||||||||||||||||||||||||||||||||||||||||||||||||||||||||||||||||||||||||||||||||||||||||||
61 | Where alarms are displayed as group alarms, provision shall be made to identify each alarm at the central control location. | |||||||||||||||||||||||||||||||||||||||||||||||||||||||||||||||||||||||||||||||||||||||||||||||||
62 | For the detection of transient faults that are subsequently self-correcting, alarms shall lock in until they are accepted. | |||||||||||||||||||||||||||||||||||||||||||||||||||||||||||||||||||||||||||||||||||||||||||||||||
63 | The alarm system shall be capable of being tested during normal machinery operation. | |||||||||||||||||||||||||||||||||||||||||||||||||||||||||||||||||||||||||||||||||||||||||||||||||
64 | Disconnection or manual overriding of any part of the alarm system shall be clearly indicated. | |||||||||||||||||||||||||||||||||||||||||||||||||||||||||||||||||||||||||||||||||||||||||||||||||
Remote Monitoring Indicators | ||||||||||||||||||||||||||||||||||||||||||||||||||||||||||||||||||||||||||||||||||||||||||||||||||
65 | Where applicable and subject to item 66, the following monitors and audible and visual alarms shall be fitted at the central control location:
| |||||||||||||||||||||||||||||||||||||||||||||||||||||||||||||||||||||||||||||||||||||||||||||||||
66 | For ships of 150 tons gross tonnage and less, only the following monitors and alarms shall be fitted at the bridge control location:
| |||||||||||||||||||||||||||||||||||||||||||||||||||||||||||||||||||||||||||||||||||||||||||||||||
Ships Exempted From Carrying Watchkeeping Engineers | ||||||||||||||||||||||||||||||||||||||||||||||||||||||||||||||||||||||||||||||||||||||||||||||||||
67 | Ships exempted from carrying watchkeeping engineers under the Safe Manning Regulations where at least one engineer is required to be aboard shall be
|
PART II(Section 6)Plans
Item | Required Information |
---|---|
1 | General arrangement of remote control and monitoring systems showing all connected machinery. |
2 | General arrangement of control and monitoring systems, including scanning points and control locations for periodically unattended machinery spaces. |
3 | General arrangement of remote control console identifying control and monitoring instruments, gauges and alarms. |
4 | Details of electric, pneumatic or hydraulic operational control and monitoring systems, and details of emergency operation arrangements for all machinery required for, or which may affect, the operational safety of the ship and safety of personnel on board. |
5 | Details of remotely controlled fire detection, alarm and extinguishing systems. |
6 | List of monitor and audio and visual alarm locations and identification of the equipment used and the manufacturer of the equipment. |
7 | General arrangement of intercommunication systems linking the bridge, accommodation spaces, service spaces, the central control room and machinery spaces, including the emergency situation alarm for engineers. |
8 | List of symbols and abbreviations used in plans in accordance with a recognized and identified code or fully explained in the data supplied. |
9 | Operational, maintenance and testing procedure manuals for control, monitoring, alarm and safety devices including duplicate and emergency arrangements. |
10 | Data indicating proposed duration of times in a 24-hour period when machinery spaces of Category A will normally be unoccupied and when other machinery spaces, such as steering gear compartments, will not normally be visited. |
11 | Data indicating surveillance arrangements on Groups 1 and 2 ships when operating in confined waters. |
12 | Data indicating security arrangements to prevent unauthorized actions in periodically unattended machinery spaces. |
PART III(Subsection 12(2))Construction and Installation Inspections
DIVISION IConstruction Inspection
Item | Requirements |
---|---|
1 | None. |
DIVISION iiInstallation Inspection
Item | Requirements |
---|---|
1 | Identification from component inspection certificates before installation is commenced of materials and components. |
2 | Witnessing of pressure testing of components as required in accordance with rules or codes. |
3 | Verification of correct adjustment and operational condition of securing arrangements and connection of the remote control and monitoring systems to associated systems. |
4 | Witnessing of operational tests of the systems including emergency and simulated fault test arrangements in accordance with rules and codes. |
PART IVPeriodic General Inspections and Periodic Special Inspections
DIVISION I(Section 19)Periodic General Inspection
Item | Requirements |
---|---|
1 | Inspection of all securing arrangements and points where leakages and excessive vibration may occur at all control locations and at the machinery itself. |
2 | Inspection of connecting systems between control locations and the machinery without complete removal of all protective panels if |
| |
3 | Witnessing of tests including emergency and simulated fault tests to confirm that all control, monitoring, alarm and safety devices are in operational condition and correct adjustment. |
4 | Witnessing of tests to confirm that systems are operable from all control locations and that the machinery is operable locally. |
5 | Witnessing of tests to confirm that duplicate and emergency systems can be rapidly brought into operation on failure of the main system. |
DIVISION II(Section 20)Periodic Special Inspection
Item | Requirements |
---|---|
1 | Subject to paragraph 20(2)(b) of these Regulations, no periodic special inspection is required. |
- SOR/2015-161, ss. 17, 18(F), 19(F), 20(E)
- SOR/2017-14, s. 411
SCHEDULE IXNon-Structural Tanks, Short Flexible Hoses and Rigid Plastic and Fibre-Reinforced Plastic Piping and Components
PART I(Section 4)Design Specifications
DIVISION IApplication
Item | Application |
---|---|
1 | This Schedule applies to non-structural tanks having a capacity of 4 500 L or less. |
2 | Non-structural tanks having a capacity of more than 4 500 L shall be designed, constructed and installed in accordance with the Hull Construction Regulations. |
DIVISION iiSpecifications
Item | Requirements |
---|---|
Non-Structural Tanks of 4 500 L or Less Capacity | |
1 | Non-structural tanks shall
|
2 | Unsupported flat surface areas for different thickness plates of non-structural tanks shall be determined by interpolation or extrapolation. |
3 | Depending on the size and configuration of a non-structural tank, the tank may be required to be fitted with baffles. |
Short Flexible Hoses | |
4 | Short flexible hoses shall be used where expansion and vibration may be encountered. |
5 | Short flexible hoses shall not be used in the correction of misalignment, except for connection of boiler fuel burners and other removable components. |
6 | Guards shall be fitted on large diameter pipes to reduce the flow of fluid leakage to within the capacity of the space bilge pumps. |
7 | Guards shall be fitted to prevent contact of leaking fluid with surfaces where a hazard may result. |
8 | Short flexible hoses shall be adequate for intended use. |
Rigid Plastic and Fibre Reinforced Plastic Piping and Components | |
9 | Except in accommodation spaces, service spaces and control locations, piping and components of rigid plastic or fibre reinforced plastic may be used in
|
10 | Piping and components of rigid plastic or reinforced plastic shall not be used
|
10.1 | Despite items 9 and 10, plastic piping referred to in sections 114 and 226 of the Vessel Fire Safety Regulations may be used. |
11 | Piping and components of rigid plastic or reinforced plastic shall be protected from
|
12 | Allowance shall be made for expansion in piping systems. |
13 | Sea inlet and overboard discharge valves shall be of suitable metal construction where connected to rigid plastic or fibre reinforced plastic piping and the piping shall not be installed outboard of the valves. |
14 | When passing through a steel water-tight or fire control bulkhead, a steel spool-piece shall be attached to the bulkhead or deck and, at a water-tight bulkhead or deck a metallic shut-off valve shall be installed immediately adjacent to the spool-piece except that no valve is required on ballast or fresh water piping located within ballast or fresh water tanks. |
15 | Remote controls operable from above the bulkhead deck shall be fitted to the shut-off valve except where
|
16 | When passing through a bulkhead or deck material other than steel, the installation shall be such that the fire, watertight and structural integrity of the bulkhead or deck is not diminished due to penetration. |
PART II(Section 6)Plans
Item | Required Information |
---|---|
Non-Structural Tanks of 4 500 L or Less Capacity | |
1 | General arrangement of the tank installation and the system to which it is connected. |
2 | Details of
|
3 | Detailed strength calculations where
|
Short Flexible Hoses | |
4 | Material specifications including details of construction and end connection arrangements. |
5 | Details of the various tests applied to the hoses and identification of the standards association whose testing standards were applied. |
6 | Details of the design working pressures, temperatures, fluid flow velocities and nature of the fluids to be carried. |
Rigid Plastic and Fibre-Reinforced Plastic Piping and Components | |
7 | Material specifications, physical properties, details of the various tests carried out and identification of the standards association whose testing standards were applied. |
8 | Characteristics of flammability, decomposition resistance to environmental conditions and abrasion resistance to sand, ice particles or other fluid entrained substances. |
9 | Details of connections, scantlings, design working pressures, temperatures and fluid flow velocities. |
10 | Details of piping systems, locations, supports and thermal expansion allowances taking into account differences in the thermal expansion properties of plastic materials and metal. |
PART III(Subsection 12(2))Construction and Installation Inspections
Item | Requirements |
---|---|
1 | Construction and installation inspections shall consist of completion of each item set out in Part III of Schedules X to XV for the relevant fluid system. |
PART IVPeriodic General Inspections and Periodic Special Inspections
DIVISION I(Section 19)Periodic General Inspection
Item | Requirements |
---|---|
1 | Completion of each item set out in Division I of Part IV of Schedules X to XV for the relevant fluid system. |
DIVISION IIPeriodic Special Inspection
SUBDIVISION I(Subsection 20(1))Parts to be Inspected
Item | Requirements |
---|---|
1 | No periodic special inspection is required if a general examination shows that the condition of the tanks is suitable for further service. |
SUBDIVISION II(Subsection 20(2))Intervals
Item | Requirements |
---|---|
1 | None. |
- SOR/2015-161, ss. 21(F), 22 to 24(E)
- SOR/2017-14, s. 415
SCHEDULE XSteam, Boiler Water and Cooling Water Systems
PART I(Section 4)Design Specifications
Item | Requirements |
---|---|
1 | Steam pipes and connected components through which steam passes shall be designed, constructed and installed to withstand the maximum working stresses to which they may be subjected. |
2 | Means shall be provided for draining every steam pipe in which dangerous water-hammer action may occur. |
3 | Where a steam pipe or component may receive steam from any source at a higher pressure than that for which it is designed, it shall be fitted with a suitable reducing valve, relief valve and pressure gauge. |
4 | Each steam generating system that provides services essential for the safety of the ship, or that could be rendered dangerous by the failure of its feed-water supply shall be fitted with at least two separate feed- water systems, including feed pumps, but a single penetration of the steam drum is acceptable. |
5 | Unless over-pressure is prevented by the pump characteristics, means shall be provided to prevent over-pressure in any part of the system. |
PART II(Section 6)Plans
Item | Required Information |
---|---|
Steam and Exhaust Systems | |
1 | General arrangement of the steam systems having an assigned working pressure in excess of 103 kPa including steam power, steam heating, steam cleaning and steam fire-extinguishing systems showing all connected pressure vessels, pumps, shut-off valves, piping, steam traps, reducing valves, safety valves, pressure gauges and drainage arrangements, particularly where the systems are susceptible to frost or water-hammer damage. |
2 | General arrangement of exhaust steam piping from machinery or other components powered or heated by steam systems referred to in item 1 showing arrangements for further use, condensing or atmospheric discharge. |
3 | Installation details of items 1 and 2 stating assigned working pressures, temperatures and flow rates. |
4 | Materials, sizes, capacities, design working pressures, temperatures, testing arrangements and procedures of pumps, piping, valves and other components. |
5 | Details of
|
6 | Information for valves and similar minor fittings referred to in item 4 is not required to be submitted where a manufacturer or an approved classification society certifies that the types of valves or similar minor fittings have been designed and constructed in accordance with rules or codes. |
7 | Information for pumps referred to in item 4 is not required to be submitted where an approved classification society certifies that the pumps have been designed and constructed in accordance with rules or codes except that the driving motor or engine of the pumps shall meet the requirements of Part II of the applicable schedule of Schedules I to XV. |
Condensate and Boiler Feed Water Systems | |
8 | General arrangement of condensate and reserve boiler feed water systems including reserve feed tank and observation tank connections, pumps, piping, valves, and all connected components and means for
|
9 | General arrangement of boiler feed, blow down and surface blow piping indicating all connected pumps, valves, components and shipside connections. |
10 | Structural details of tanks that do not form part of the hull structure. |
11 | Installation details of items 8 and 9 stating assigned working pressures, temperatures and flow rates. |
12 | Materials, sizes, design working pressures, testing arrangements and procedures of pumps, piping, valves and other components. |
13 | Details of
|
14 | Information for valves and similar minor components referred to in item 12 is not required to be submitted where a manufacturer or an approved classification society certifies that the types of valves or similar minor components have been designed and constructed in accordance with rules or codes. |
15 | Information for pumps referred to in item 12 is not required to be submitted where an approved classification society certifies that the pumps have been designed and constructed in accordance with rules or codes except that the driving motor or engine of the pumps shall meet the requirements of Part II of the applicable schedule of Schedules I to XV. |
Cooling Water Systems | |
16 | General arrangement of fresh and seawater cooling systems pumps, piping, valves and components including, as applicable, sea suction strainers, air vent piping, sea boxes, internal sea bays, keel coolers, ship structure tank coolers, make-up water tanks and means for draining systems that are susceptible to frost damage. |
17 | Details of sea inlet and discharge arrangements including arrangements to ensure that no above waterline discharges are in the way of lifeboat and liferaft lowering locations and, where applicable, piping arrangements for internal sea bays, keel coolers and ship structure tank coolers. |
18 | Structural details of tanks not forming part of the hull structure. |
19 | Installation details of all water systems referred to in item 16 stating assigned working pressures, temperatures and flow rates. |
20 | Materials, sizes, design working pressures, testing arrangements and procedures of pumps, piping, valves and other components. |
21 | Details of
|
22 | Information for valves and similar minor components referred to in item 20 is not required to be submitted where a manufacturer or an approved classification society certifies that the types of valves or similar minor components have been designed and constructed in accordance with rules or codes. |
23 | Information for pumps referred to in item 20 is not required to be submitted where an approved classification society certifies that the pumps have been designed and constructed in accordance with rules or codes except that the driving motor or engine of the pumps shall meet the requirements of Part II of the applicable schedule of Schedules I to XV. |
PART III(Subsection 12(2))Construction and Installation Inspections
DIVISION IConstruction Inspection
Item | Requirements |
---|---|
1 | None. |
DIVISION IIInstallation Inspection
Item | Requirements |
---|---|
1 | Identification from component inspection certificates, before installation is commenced, of pumps, piping, flexible hoses, components and materials to be used, including welding metal. |
2 | Verification that welding was carried out by welders certified by a Provincial Government of Canada, or another authority having similar standards where the welding was carried out outside Canada, for the class of work to be done. |
3 | Inspection of welds and verification of the heat treatment process in accordance with rules or codes. |
4 | Witnessing of hydrostatic pressure tests in accordance with rules or codes. |
5 | Inspection of securing arrangements, connections with associated systems and verification of correct adjustment and operational condition of safety, control and monitoring devices. |
6 | Witnessing of operational tests of the system in accordance with rules or codes. |
PART IVPeriodic General Inspections and Periodic Special Inspections
DIVISION I(Section 19)Periodic General Inspection
Item | Requirements |
---|---|
1 | For steam and exhaust systems, where applicable and, in the opinion of the inspector, practicable,
|
2 | For boiler water and cooling water systems, where applicable and, in the opinion of the inspector, practicable,
|
3 | For pumps, where applicable and, in the opinion of the inspector, practicable,
|
DIVISION IIPeriodic General Inspection
SUBDIVISION I(Subsection 20(1))Parts to be Inspected
Item | Requirements |
---|---|
1 | Except as prescribed in Schedules I to III, safety valves, pressure gauges and other components in steam, boiler water and cooling water systems and reducing valves in steam systems are to be inspected without opening up unless considered necessary by the inspector on the basis of the general condition of the steam, boiler water and cooling water systems. |
2 | Subject to items 3 to 6, steam piping systems that have an external diameter in excess of 75 mm shall have selected pipes removed for
|
3 | Pipes selected for inspection shall be different from the pipes selected during the previous inspection so that in the course of successive inspections all pipes of the system are inspected and tested. |
4 | Steam piping that has an external diameter in excess of 75 mm and that has welded joints between lengths of pipe or between pipes and valves shall have
|
5 | All copper steam pipes that have an external diameter in excess of 75 mm, shall be subjected to a hydrostatic pressure test of twice the assigned working pressure of the system and all seams, including longitudinal seams where fitted, exposed for inspection. |
6 | Copper steam pipes that have an external diameter in excess of 75 mm and that are subject to flexing action through expansion or vibration and copper steam piping immediately adjacent to machinery shall be removed for annealing prior to being hydrostatically pressure tested in accordance with subitem 2(c). |
7 | For pumps and driving components, where applicable,
|
8 | For shipside sea inlet valves, strainers, overboard discharge valves and valves connected to internal sea bays, keel coolers, reserve feed water tanks and observation tanks,
|
9 | No inspection is required for speed regulating governors and other complex mechanisms where written information is provided to the inspector from firms specializing in the reconditioning of these parts indicating that the parts are in good order and adjustment. |
SUBDIVISION II(Subsection 20(2))Intervals
Item | Requirements |
---|---|
1 | Components listed in item 1 of Subdivision I, at intervals not exceeding five years. |
2 | Subject to item 3, superheated steam pipes, at intervals not exceeding four years. |
3 | Saturated steam pipes and superheated steam pipes that have an external diameter of less than 75 mm and not subject to temperatures exceeding 450°C, eight years after installation and thereafter at intervals not exceeding four years. |
4 | Pumps and driving components, at intervals not exceeding five years. |
- SOR/2015-161, ss. 25(E), 26(F)
SCHEDULE XICompressed Air and Refrigerating Gas Systems
PART I(Section 4)Design Specifications
Item | Requirements |
---|---|
1 | Means shall be provided to prevent over-pressure in any part of compressed air and refrigerating gas systems and in water jackets or casings of compressors and coolers that may be subjected to over-pressure due to pressurized air or gas leakage. |
2 | Where necessary, engine starting compressed air arrangements shall be adequately protected against the effects of backfiring and internal explosion in the starting air pipes. |
3 | All discharge pipes from starting air compressors shall lead directly to the starting air receivers, and all starting pipes from the air receivers to main or auxiliary engines shall be entirely separate from the compressor discharge piping system. |
4 | Means shall be provided to reduce to a minimum the entry of oil into the air pressure systems and to drain those systems. |
5 | Where soldering is to be used for piping connections, the metal shall be silver solder. |
PART II(Section 6)Plans
Item | Required Information |
---|---|
Compressed Air Systems | |
1 | General arrangement of unfired pressure vessels, compressors, air-driven machinery, valves, piping, moisture traps, reducing valves, safety valves, pressure gauges and drainage arrangements, particularly where susceptible to frost damage. |
2 | Installation details indicating assigned working pressures, temperatures and flow rates. |
3 | Materials, sizes, capacities, design working pressures, temperatures, testing arrangements and procedures of compressors, air driven machinery, piping, valves and other components. |
4 | Details of
|
5 | Information set out in items 1 to 4 is not required to be submitted for
|
6 | Information for valves and similar minor components referred to in item 3 is not required to be submitted where a manufacturer or an approved classification society certifies that the types of valves or similar minor components have been designed and constructed in accordance with rules or codes. |
7 | Information for compressors or air driven machinery referred to in item 3 is not required to be submitted where an approved classification society certifies that the compressors or air driven machinery have been designed and constructed in accordance with rules or codes except that the driving or driven components shall meet the requirements of Part II of the applicable schedule of Schedules I to XV. |
Refrigerating Gas Systems | |
8 | General arrangement and location of compressors, valves, driers, strainers, oil separators, safety devices, sight glasses, piping, temperature and pressure gauges, alarms, condensers, liquid receivers, evaporation arrangements, refrigerated and air conditioned spaces. |
9 | Installation details indicating assigned working pressures, temperatures and capacities. |
10 | Materials, sizes, capacities, design working pressures, temperatures, testing arrangements and procedures of compressors, piping, valves and other components. |
11 | Details of
|
12 | Information set out in items 8 to 11 is not required to be submitted for
|
13 | Information for valves and similar minor components referred to in item 10 is not required to be submitted where a manufacturer or an approved classification society certifies that the types of valves or similar minor components have been designed and constructed in accordance with rules or codes. |
14 | Information for compressors referred to in item 10 is not required to be submitted where an approved classification society certifies that the compressors have been designed and constructed in accordance with rules or codes except that the driving motors or engines of the compressors shall meet the requirements of Part II of the applicable schedule of Schedules I to XV. |
PART III(Subsection 12(2))Construction and Installation Inspections
DIVISION IConstruction Inspection
Item | Requirements |
---|---|
1 | None. |
DIVISION IIInstallation Inspection
Item | Requirements |
---|---|
1 | Identification from component inspection certificates, before installation is commenced, of compressors, piping, flexible hoses, components and materials to be used, including welding or brazing metal. |
2 | Verification that welding was carried out by welders certified by a Provincial Government of Canada, or another authority having similar standards where the welding was carried out outside Canada, for the class of work to be done. |
3 | Inspection of welds. |
4 | Witnessing of hydrostatic pressure tests and for a refrigerating gas system, verification that gas leak testing has been satisfactorily carried out in accordance with rules or codes. |
5 | Inspection of securing arrangements of compressors and heat exchangers, connection of piping to associated systems and verification of correct adjustment and operational condition of safety, control and monitoring devices. |
6 | Witnessing of operational tests of the system in accordance with rules or codes. |
7 | Items 1 to 6 do not apply to
|
PART IVPeriodic General Inspections and Periodic Special Inspections
DIVISION I(Section 19)Periodic General Inspection
Item | Requirements |
---|---|
1 | For air and refrigerating gas compressors and air-driven machinery, where applicable and, in the opinion of the inspector, practicable, verification that the compressors, air-driven machinery, cooling systems, control, monitoring alarm and safety devices are in correct adjustment and operational condition. |
2 | For compressed air and refrigerating gas piping systems, where applicable and, in the opinion of the inspector, practicable,
|
3 | Items 1 and 2 do not apply to
|
DIVISION IIPeriodic Special Inspection
SUBDIVISION I(Subsection 20(1))Parts to be Inspected
Item | Requirements |
---|---|
1 | For compressed air systems
|
2 | Item 1 does not apply to non-essential ship systems containing compressed air and having an assigned working pressure of not less than 103 kPa. |
3 | No periodic special inspection is required for complex mechanisms where written information is provided to the inspector from firms specializing in the reconditioning of these parts indicating that the parts are in good order and adjustment. |
SUBDIVISION II(Subsection 20(2))Intervals
Item | Requirements |
---|---|
1 | At intervals not exceeding five years. |
SCHEDULE XIIFuel Oil Systems
PART I(Section 4)Design Specifications
Item | Requirements |
---|---|
1 | Subject to items 2 and 3, fuel oil for all fixed installations shall have a flash-point of not less than 60°C (closed cup test). |
2 | Fuel oil for fixed installations may have a flash-point of not less than 43°C (closed cup test) where
|
3 | Fuel oil for emergency generator service may have a flash-point of not less than 43°C (closed cup test). |
4 | Fixed fuel oil systems for helicopters and for non-fixed equipment shall have additional safety features taking into account the quantity of fuel carried and the hazardous properties of the fuel. |
5 | Small approved portable containers holding fuel oil with a flash-point of lower than 43°C shall
|
6 | For ships operating in extremely cold conditions with exposed fuel oil piping to the emergency generator from an external deck-mounted fuel tank, means shall be taken so that the fuel oil viscosity will not adversely affect oil flow and where warming systems are used, the system shall incorporate a heat-limiting device to ensure that the oil is not heated to a temperature exceeding 20°C. |
7 | The ventilation of spaces in which fuel oil is used shall be sufficient to prevent accumulation of oil vapour. |
Tanks | |
8 | Fuel oil shall not be stored in the forepeak and the tanks shall, as far as practicable, form part of the ship structure. |
9 | Where fuel oil tanks, except double bottom tanks, are located adjacent to machinery spaces of category A out of necessity, they shall have a common boundary, where practicable, with the double bottom tanks, and the area of the tank boundary common with the machinery spaces of category A shall be kept to a minimum. |
10 | Where practicable, the use of non-structural fuel oil tanks shall be avoided, but where used such tanks shall
|
11 | No fuel oil tank shall be located where spillage or leakage from the tank creates a hazard by falling on heated surfaces. |
12 | Fuel oil tanks for cooking and cabin hot-air heating appliances shall not be installed in the same spaces as the appliances and the supply of oil to appliance burners shall be capable of being shut off from positions outside the spaces in which the appliances are fitted. |
13 | Quantities of fuel oil in tanks may be determined by
|
14 | Where fuel oil quantities in a tank are determined by means other than sounding pipes, the installation of the system shall be in accordance with the following requirements:
|
15 | Provision shall be made to prevent over-pressure in any fuel tank or system by means of
|
16 | Subject to item 17, every fuel oil pipe that if damaged would allow fuel oil to escape either by gravity or siphon action from a storage, settling or daily service tank located in a space above the double bottom shall be fitted with a cock or valve on the tank that is capable of being closed from a safe location outside the space. |
17 | In the case of deep tanks situated in any shaft or pipe tunnel or similar compact space, valves shall be fitted on the tanks and remote control may be operated by means of an additional valve outside the compact space. |
18 | Where an additional valve is fitted in the machinery space it shall be operable from outside that space. |
Piping and Components | |
19 | As far as practicable, all parts of a fuel oil system containing heated oil under pressure exceeding 180 kPa shall be located so that defects and leakage can be readily observed. |
20 | Machinery space fuel oil piping and components shall be adequately illuminated. |
21 | Means shall be provided to prevent oil that may escape under pressure from a component from coming into contact with heated surfaces. |
22 | Drip trays with drains leading to a sludge oil tank shall be fitted under all components where leakage may occur. |
23 | Fuel oil pipes shall be of steel or similar fire and pressure-resistant material, except that short flexible hoses may be used in accordance with Schedule IX. |
24 | Flexible hoses and end attachments shall be of fire-resistant materials of adequate strength and shall be constructed in accordance with Schedule IX. |
Incinerators, Cooking Ranges and Cabin Hot-Air Heating Appliances | |
25 | Printed manufacturer’s instructions for the proper installation, maintenance and operation of each fuel oil burning appliance shall be permanently mounted in a visible location adjacent to the appliance. |
26 | In addition to the instructions referred to in item 25, the following safety instructions shall be prominently posted in spaces, other than machinery spaces, where fuel oil burning appliances are located: “WARNING ENSURE THAT FRESH AIR VENTILATION SYSTEM IS IN OPERATION WHEN USING FUEL-BURNING APPLIANCE If leakage of fuel oil is suspected or detected, the following actions must be taken immediately:
|
PART II(Section 60)Plans
Item | Required Information |
---|---|
1 | General arrangement and location of permanently installed fuel oil systems including connections to boilers, engines, heat exchangers, incinerators, cooking ranges, cabin hot-air heaters, pumps, purifiers, filters, valves, pressure gauges, piping, filling stations, tanks, tank sounding devices, flame-screened venting and overflow arrangements, drip trays and sludge facilities and oil pollution prevention components. |
2 | Structural details of fuel oil tanks not forming part of the hull structure and of not more than 4 500 L capacity. |
3 | Installation details indicating assigned working pressures, temperatures, flow rates and the oil flash-point (closed cup test). |
4 | Materials, sizes, capacities, design working pressures, temperatures, testing arrangements and procedures of incinerators, pumps, purifiers, filters, valves, tank sounding and venting devices, piping and other components. |
5 | Details of
|
6 | Information set out in items 3 to 5 need not be submitted for ships not in excess of 18 m in length. |
7 | Information for valves and similar minor components referred to in item 4 is not required to be submitted where a manufacturer or an approved classification society certifies that the types of valves or similar minor components have been designed and constructed in accordance with rules or codes. |
8 | Information for pumps or purifiers referred to in item 4 is not required to be submitted where an approved classification society certifies that the pumps or purifiers have been designed and constructed in accordance with rules or codes except that the driving motor or engine of pumps shall meet the requirements of Part II of the applicable schedule of Schedules I to XV. |
PART III(Subsection 12(2))Construction and Installation Inspections
DIVISION IConstruction Inspection
Item | Requirements |
---|---|
1 | None. |
DIVISION IIInstallation Inspection
Item | Requirements |
---|---|
1 | Identification from component inspection certificates, before installation is commenced, of pumps, appliances, piping, tank sounding and venting devices, flexible hoses, materials, including weld metal, oil pollution prevention equipment and other components to be used. |
2 | Verification that welding was carried out by welders certified by a Provincial Government of Canada, or another authority having similar standards where the welding was carried out outside Canada, for the class of work to be done. |
3 | Inspection of welds. |
4 | Witnessing of hydrostatic pressure tests in accordance with rules or codes and verification of system flushing. |
5 | Inspection of securing arrangements of pumps, heat exchangers and appliances, connection of piping to associated systems and verification of correct adjustment and operational condition of safety, control and monitoring devices. |
6 | Witnessing of operational tests of the system in accordance with rules or codes. |
PART IVPeriodic General Inspections and Periodic Special Inspections
DIVISION I(Section 19)Periodic General Inspection
Item | Requirements |
---|---|
1 | Where applicable and, in the opinion of the inspector, practicable,
|
DIVISION IIPeriodic Special Inspection
SUBDIVISION I(Subsection 20(1))Parts to be Inspected
Item | Requirements |
---|---|
1 | External and internal parts of pumps and driving components including valves, bearings, control and safety devices, except gear or rotary pumps where dismantling is not required if a general examination shows that the condition of components is suitable for further service. |
2 | Systems shut-off valves, safety devices and other components without dismantling if a general examination shows that the condition of the components is suitable for further service. |
3 | Securing arrangements of components without dismantling if a general examination shows that the condition of the securing arrangements is suitable for further service. |
4 | No special periodic inspection is required for complex mechanisms where written information is provided to the inspector from firms specializing in the reconditioning of these parts that the parts are in good order and adjustment. |
SUBDIVISION II(Subsection 20(2))Intervals
Item | Requirements |
---|---|
1 | At intervals not exceeding five years. |
- SOR/95-372, s. 7(F)
- SOR/2015-161, ss. 27(F), 28(E)
SCHEDULE XIIILiquefied Petroleum Gas Fuel Systems
PART I(Section 4)Design Specifications
DIVISION IApplication
Item | Description of Appliances |
---|---|
1 | This Schedule applies to the following galley and cabin-heating appliances aboard non-passenger ships:
|
DIVISION IISpecifications
Item | Requirements |
---|---|
1 | Gas fuel shall have a distinctive odour to indicate the presence of gas down to a concentration of 20 per cent of the lower explosive limit of the gas in the air. |
2 | No liquefied petroleum gas fuel system of a type other than the vapour withdrawal type shall be installed or used in a ship. |
3 | Gas fuel cylinders and regulating and safety devices shall be securely fastened and so located that escaping vapour cannot reach bilges, machinery spaces, accommodation or other enclosed spaces. |
4 | Location of gas fuel cylinders, regulation arrangements and relief valve outlets shall be located only on open decks, on cabin tops, outside cockpits or inside housings that are gas-tight to the hull interior. |
5 | Appliances shall be installed in accordance with the manufacturer’s instructions and shall be securely fastened. |
6 | Appliances shall be connected in a manner that prevents undue strain on the piping. |
7 | Only liquefied petroleum gas fuel cylinders that meet the requirements of the Transport of Dangerous Goods Directorate of the Department of Transport or the Interstate Commerce Commission of the United States shall be used. |
8 | Liquefied petroleum gas fuel system components and piping shall have a design working pressure of not less than 1 725 kPa. |
Piping Systems | |
9 | Gas fuel piping shall
|
10 | Gas fuel piping shall not be used as part of any electrical circuit or grounding system. |
11 | Gas fuel piping shall not be used as support or restraint for any item or fitting that is not part of the gas system. |
12 | Any valves, regulators or other fittings exceeding 0.5 kg mass per 6 mm of pipe outside diameter shall have their mass supported by means other than the gas piping. |
13 | Gas fuel piping shall be of a sufficient diameter to provide a sufficient supply of gas fuel to meet demand pressures at the point of use and the pressure drop between the regulator and the appliance shall not exceed 10 per cent. |
14 | High-pressure liquefied petroleum gas fuel piping between the gas storage cylinders and the regulators shall have a minimum wall thickness of 1.24 mm and the low-pressure gas fuel piping between the regulators and the gas-burning appliances shall have a minimum wall thickness of 0.81 mm. |
15 | Liquefied petroleum gas fuel piping shall
|
16 | Short reinforced flexible hoses and couplings used to connect the gas fuel piping system to a cylinder or gimballed appliance shall be of a type referred to in item 24. |
17 | Short reinforced flexible hoses shall be of the minimum practicable length but not longer than 1 m and shall not extend from one cabin to another or pass through any bulkheads, partitions, deck heads or decks. |
Gas Storage Cylinders | |
18 | No gas fuel storage cylinder that permits gas in liquid form to enter any other part of the gas system shall be used. |
19 | Each liquefied petroleum gas fuel storage cylinder shall have a manually operated screw-down shut-off valve mounted directly on the cylinder outlet. |
20 | The manually operated screw-down shut-off valve shall be fitted with a spring-loaded safety device and with a fusible plug designed to yield when the cylinder has been emptied of liquefied petroleum gas by the relief valve under exposure to excessive heat. |
21 | The shut-off valve, the spring-loaded safety device and the fusible plug referred to in item 20 shall each have direct communication with the vapour space of a gas fuel storage cylinder. |
22 | A multiple-cylinder gas fuel system shall be fitted with a manually operated two-way positive shut-off manifold valve so arranged that the replacement of empty cylinders may be made without shutting down the flow of gas in the gas fuel system. |
23 | No electrical connections shall be made within a gas fuel storage cylinder enclosure. |
Gas Fuel Components and Appliances | |
24 | Except for the gas fuel storage cylinders, only gas fuel components and appliances that meet the requirements of the Canadian Gas Association, the Compressed Gas Association, the Underwriters’ Laboratories of Canada or the Underwriters’ Laboratories Incorporated shall be used. |
25 | All valves and regulators embodied in the gas fuel system for the purpose of pressure relief, regulation or control of gas pressure and flow rates shall be securely mounted in a position readily accessible for operation, inspection, maintenance and testing, and shall be protected against physical damage. |
26 | The gas fuel system shall be fitted with a regulating device adjusted to release gas to the consuming appliance at a pressure not in excess of 4.5 kPa. |
27 | The low-pressure side of all regulators in the gas fuel system shall be protected against excessive pressure by means of a suitable relief valve that is fitted to the regulator and set to discharge at a pressure of not less than twice, and not more than three times, the delivery pressure. |
28 | All regulators in the gas fuel system shall be fitted with a pressure gauge located on the high-pressure side of the regulator. |
29 | A master packless shut-off valve controlling all burners simultaneously shall be installed on the console of each gas-burning appliance. |
30 | All appliances incorporating pilot-lights or other continuous-burning flame devices shall incorporate a flame failure device arranged to shut off the main and pilot gas in the event of flame failure. |
31 | Installation clearances between appliances and adjacent combustible material shall not be less than the clearances specified in the manufacturer’s instructions. |
32 | The piping and components in the gas fuel system shall be located so that gas leakage tests may be carried out at prescribed intervals as follows:
|
Systems Installation for Ships Exceeding 24 m in Length | |
33 | Gas fuel storage cylinders and pressure-regulating and relief arrangements shall be
|
34 | Spare and empty gas fuel cylinders shall have valve outlets that are capped and may be stored within the metal enclosure or may be secured on the open deck in a location that is protected from damage, direct rays of the sun and heat by a suitable cover, and the enclosure or cover shall be ventilated to prevent the accumulation of gas. |
35 | The metal enclosure shall be designed to be closed at all times except when access is required to change cylinders in the gas system or to maintain equipment, and only the following items shall be stored in the enclosure:
|
36 | Gas fuel storage cylinder pressure-relief valves shall be vented away from the cylinders and, as far as practicable, upwards to prevent impingement of escaping gas onto the cylinders. |
37 | Gas fuel safety device vent outlets shall end at least 1.5 m from enclosed space openings and ventilation intakes. |
38 | Compartments containing liquefied petroleum gas-burning appliances that are located above the weather deck shall be ventilated by
|
39 | Compartments that contain liquefied petroleum gas-burning appliances or in which gas may accumulate and that are located entirely below the weather deck shall be ventilated by mechanical ventilation of the positive extraction type with a spark-proof fan and motor having sufficient capacity to effect at least 10 air changes per hour through ventilators leading to and from the open deck and the extraction duct of the ventilator shall extend from the deck level and the inlet duct of the ventilator shall extend to the deckhead of the compartment. |
Systems Installation for Ships not Exceeding 24 m in Length | |
40 | Gas fuel storage cylinders and pressure-regulating and relief arrangements shall be
|
41 | Gas fuel storage cylinder pressure-relief valves shall be vented away from the cylinders, and, as far as practicable, upwards to prevent impingement of escaping gas onto the cylinders. |
42 | Gas fuel safety device vent outlets from safety devices shall end as far as practicable from enclosed space openings and ventilation intakes. |
43 | Spare and empty gas fuel cylinders shall have capped valve outlets, and shall be secured on the open deck and protected from damage, direct rays of the sun and heat. |
44 | Compartments that contain gas-burning appliances or in which gas may accumulate shall be efficiently ventilated so that inside air is exhausted through a vent opening located at the lowest part of the compartments. |
Safety Notices for All Ships | |
45 | Printed manufacturer’s instructions for the proper installation, maintenance and operation of each gas-burning appliance shall be permanently mounted in a readily visible location adjacent to the appliance. |
46 | The gas fuel cylinder storage location shall prominently display the following warning and operating instructions: “WARNING LIQUEFIED PETROLEUM GAS FUEL NO OPEN FLAME NO SMOKING BEFORE TURNING ON GAS FUEL READ OPERATING INSTRUCTIONS BELOW KEEP CYLINDER VALVES CLOSED WHEN CYLINDER EMPTY OR SHIP IS UNATTENDED BE SURE ALL APPLIANCE VALVES ARE CLOSED BEFORE OPENING THE CYLINDER VALVES CLOSE APPLIANCE VALVES WHEN APPLIANCE IS NOT IN USE TEST SYSTEM FOR LEAKAGE AT LEAST TWICE A MONTH CONSUMER OPERATING INSTRUCTIONS
|
47 | The following warning and safety instructions shall be prominently posted in spaces where gas fuel appliances are located: “WARNING ENSURE THAT FRESH AIR VENTILATION SYSTEM IS IN OPERATION WHEN USING FUEL-BURNING APPLIANCE
|
PART II(Section 6)Plans
Item | Required Information |
---|---|
1 | General arrangement and location of the complete system including gas fuel cylinders, components, piping, appliances, venting and safety arrangements. |
2 | Installation details stating assigned working pressures, materials and sizes of cylinders, components, piping and appliances. |
3 | Details of
|
4 | Data indicating the authority referred to in items 7 and 24 of Division II of Part I for cylinders, components and appliances. |
5 | Information set out in items 1 to 4 is not required to be submitted for ships not exceeding 24 m in length. |
PART III(Subsection 12(2))Construction and Installation Inspections
DIVISION IConstruction Inspection
Item | Requirements |
---|---|
1 | None. |
DIVISION IIInstallation Inspection
Item | Requirements |
---|---|
1 | Identification from component inspection certificates, before installation is commenced, of gas fuel storage cylinders, components, piping, flexible hoses, appliances and vent fans. |
2 | Inspection of securing arrangements, protective housings, component and piping connections, venting arrangements, all safety devices and arrangements. |
3 | Witnessing of gas fuel pressure and leakage tests as follows:
|
4 | Witnessing of operational tests of the system and verification that safety and operating instructions are posted in accordance with items 44 and 45 of Division II of Part I. |
PART IVPeriodic General Inspections and Periodic Special Inspections
DIVISION I(Section 19)Periodic General Inspection
Item | Requirements |
---|---|
1 | Inspection of securing arrangements and for evidence of gas fuel leakage. |
2 | Verification that all components and venting systems are in correct adjustment and operational condition. |
3 | Verification that safety and operating instructions are correctly posted. |
DIVISION IIPeriodic Special Inspection
SUBDIVISION I(Subsection 20(1))Parts to be Inspected
Item | Requirements |
---|---|
1 | Entire gas fuel systems
|
2 | Securing arrangements of gas fuel systems without dismantling if a general examination shows that the condition of components is suitable for further service. |
3 | Gas cylinders to verify that they have been tested in accordance with the requirements of the Transport of Dangerous Goods Directorate of the Department of Transport. |
4 | A gas fuel storage cylinder shall be rejected for further service regardless of the date of its previous test if it
|
5 | Fans and ducting of venting systems to verify that they are suitable for the required use. |
SUBDIVISION II(Subsection 20(2))Intervals
Item | Requirements |
---|---|
1 | At intervals not exceeding five years. |
- SOR/2015-161, ss. 29(E), 30(E), 31(F)
SCHEDULE XIVLubricating Oil and Hydraulic Power Oil Systems
PART I(Section 4)Design Specifications
Item | Requirements |
---|---|
1 | Where the ship is to operate in low ambient temperatures, measures shall be taken to maintain essential deck machinery lubricating oil and hydraulic power oil at a viscosity suitable for reliable operation of the machinery. |
Tanks | |
2 | No lubricating oil or hydraulic power oil tank shall be located where spillage or leakage from the tanks creates a hazard by falling on heated surfaces. |
3 | No lubricating oil or hydraulic power oil shall be carried in the fore-peak. |
4 | Means shall be provided to prevent over-pressure in
|
5 | Quantities of lubricating oil or hydraulic power oil in tanks shall be determined by
|
6 | Subject to item 7, for ships certificated to carry more than 12 passengers and other ships in excess of 500 tons gross tonnage, every pressurized lubricating oil system pipe which when damaged allows oil to escape from a storage or service tank situated above the double bottom, shall be fitted with a cock or valve on the tank capable of being closed from a safe position outside the space. |
7 | In the case of tanks situated in any shaft or pipe tunnel or similar compact space, cocks or valves shall be fitted on the tanks and remote control may be operated by means of an additional valve outside the compact space. |
8 | Where the additional valve is fitted in the machinery space it shall be operable from outside this space. |
Piping and Components | |
9 | As far as practicable, all parts of a lubricating oil or hydraulic power oil system containing heated oil under pressure exceeding 180 kPa shall be located so that defects and leakage can readily be observed. |
10 | Machinery space lubricating oil and hydraulic power oil piping and components shall be adequately illuminated. |
11 | Means shall be taken to prevent oil that may escape under pressure from any component from coming into contact with heated surfaces. |
12 | Drip trays with drains leading to a sludge oil tank shall be fitted under all components where leakage may occur. |
13 | Lubricating oil and hydraulic power oil pipes shall be of steel or similar fire and pressure resistant material, except that flexible hoses are permissible in accordance with Schedule IX. |
14 | Sight flow glasses in piping systems shall be of fire resistant types. |
PART II(Section 6)Plans
Item | Required Information |
---|---|
1 | General arrangement and location of permanently installed oil systems, including connections to all applicable machinery, heat exchangers, pumps, purifiers, filters, valves, piping, filling stations, tanks, tank sounding devices, flame screened venting and overflow arrangements, drip-trays and sludge facilities and oil pollution prevention components. |
2 | Structural details of tanks not forming part of the hull structure. |
3 | Installation details indicating assigned working pressures, temperatures, flow rates, oil flash-point (closed cup test) and oil viscosity at highest and lowest operating temperatures. |
4 | Materials, sizes, capacities, design working pressures, temperatures, testing arrangements and procedures of pumps, purifiers, piping, valves and other components. |
5 | Details of
|
6 | Information set out in items 1 and 3 to 5 is not required to be submitted for
|
7 | Information for valves and similar minor fittings referred to in item 4 is not required to be submitted where a manufacturer or an approved classification society certifies that the types of valves or similar minor components have been designed and constructed in accordance with rules or codes. |
8 | Information for pumps and purifiers referred to in item 4 is not required to be submitted where an approved classification society certifies that the pumps or purifiers have been designed and constructed in accordance with rules or codes except that the driving motor or engine of pumps shall meet the requirements of Part II of the applicable schedule of Schedules I to XV. |
PART III(Subsection 12(2))Construction and Installation Inspections
DIVISION IConstruction Inspection
Item | Requirements |
---|---|
1 | None. |
DIVISION IIInstallation Inspection
Item | Requirements |
---|---|
1 | Identification from component inspection certificates, before installation is commenced, of pumps, applicable essential machinery, piping, flexible hoses, materials, including welding metal, and other components to be used. |
2 | Verification that welding was carried out by welders certified by a Provincial Government of Canada, or another authority having similar standards where the welding was carried out outside Canada, for the class of work to be done. |
3 | Inspection of welds. |
4 | Witnessing of hydrostatic pressure tests in accordance with rules or codes and verification of system flushing. |
5 | Inspection of securing arrangements of the lubricating oil and hydraulic power oil system and verification of correct adjustment and operational condition of safety, control and monitoring devices. |
6 | Witnessing of operational tests of the system in accordance with rules or codes. |
PART IVPeriodic General Inspections and Periodic Special Inspections
DIVISION I(Section 19)Periodic General Inspection
Item | Requirements |
---|---|
1 | For essential lubricating oil and hydraulic power oil systems and, in locations where oil leakage is hazardous, non-essential systems,
|
DIVISION IIPeriodic Special Inspection
SUBDIVISION I(Subsection 20(1))Parts to be Inspected
Item | Requirements |
---|---|
1 | For essential lubricating oil and hydraulic power oil systems,
|
2 | No periodic special inspection is required for complex mechanisms where written information is provided to the inspector from firms specializing in the reconditioning of these parts that the parts are in good order and adjustment. |
SUBDIVISION II(Subsection 20(2))Intervals
Item | Requirements |
---|---|
1 | At intervals not exceeding five years. |
- SOR/2015-161, ss. 32, 33(F)
SCHEDULE XVBilge and Ballast Pumping Systems, Heeling, Trimming and Passive Roll Stabilizing Tank Filling and Emptying Systems
PART I(Section 4)Design Specifications
DIVISION IApplication
Item | Description of Ships |
---|---|
1 | In this Schedule,
|
DIVISION iiGroups 1, 2 and 3 Ships
Item | Requirements |
---|---|
Pumping Systems | |
1 | Water shall be prevented from inadvertently passing from
|
2 | Piping systems shall be arranged as follows:
|
3 | Screw-down non-return valves shall be fitted in the following components:
|
4 | All cocks and valves that are connected to bilge and ballast pipes shall be fitted with legible name-plates and shall be in readily accessible positions. |
5 | For ships, other than tankers and similar ships, branch bilge suction pipes shall be connected to the main bilge suction pipes and shall be arranged to draw water from any cargo hold, tunnel, machinery space or similar compartment, except that in chain lockers and other small spaces independent pumps that are power or manually driven may be used. |
6 | Subject to items 7 and 118 to 121, bilge suction pipes that are required for drawing water from cargo or machinery spaces shall be entirely separate from sea inlet pipes or from pipes that may be used for filling or emptying spaces where water or oil is carried. |
7 | The following connections may be used in bilge suction systems:
|
8 | Ballast water shall not be carried in tanks intended for fuel oil unless required for the stability of the ship or other safety reasons. |
9 | Where tanks, including passive roll-stabilizing tanks, are arranged for alternative carriage of oil, water or dry cargo, there shall be blank flanging or other suitable arrangements to prevent interconnection of pumping, overflow or liquid heating systems. |
10 | Bilge suction pipes shall not be carried through double bottom tanks unless alternative routing is impracticable. |
11 | Bilge suction pipes that pass through double bottom tanks shall be of extra-heavy thickness. |
12 | Bilge suction pipes that pass through deep tanks shall be led through pipe tunnels, but where such leading is not practicable, the pipes shall be of extra-heavy thickness and fitted in one length if practicable, with welded or heavily flanged joints. |
13 | Provision for expansion of pipes shall be made and within tanks expansion bends only shall be fitted. |
14 | The open ends of the bilge suction pipes in the holds shall be fitted with non-return valves suitable for use in cargo holds. |
15 | The distance between the lower end of all bilge suction tailpipes and the bottom of the bilge or well shall be adequate to allow a full flow of water and to facilitate cleaning. |
16 | Bilge and ballast suction and discharge pipes shall be made in readily removable lengths with flanged joints, except as prescribed in item 12, and shall be efficiently secured in position to prevent chafing or movement. |
17 | Long or heavy lengths of pipes shall be supported by bearers so that no undue load will be carried by the flanged connections of the pumps or fittings to which the flanged connections are attached. |
18 | Subject to subitem 9(c) of Division II of Part I of Schedule IX, pipes for bilge, ballast and similar systems shall be made of steel or other metallic material. |
19 | Piping, valves, mud boxes, strainers and extended spindles, where fitted, shall be protected against damage, particularly in cargo holds where spindles shall be encased. |
20 | Shipside connections shall be designed, constructed and installed in accordance with rules or codes and Schedule VII. |
Machinery Space Normal Bilge Pumping | |
21 | The machinery space bilge-water means of drainage for normal bilge pumping shall be such that any water that enters the space can be pumped out through at least two bilge suction pipes when the ship is on an even keel and is either upright or is listing by not more than 5°. |
22 | One of the suction pipes shall be a branch bilge suction pipe leading from the main bilge suction pipe and the other shall be a direct bilge suction pipe leading directly from an independent power pump that may be used independently of the main bilge suction piping system. |
23 | Where the double bottom extends the full length of the machinery space and forms bilges at the sides of the machinery space, one branch bilge suction pipe and one direct bilge suction pipe shall lead to each side bilge. |
24 | Where the double bottom extends the full length and breadth of the machinery space and is fitted with bilge wells, one branch bilge suction pipe and one direct bilge suction pipe shall lead to each of the two bilge wells having a capacity of not less than 150 L and situated one at each side of the machinery space. |
25 | Where there is no double bottom, one branch bilge suction pipe and one direct bilge suction pipe shall lead to accessible locations as near to the centre line of the ship as practicable and, if the rise of the floor is less than 5°, a branch bilge suction pipe shall lead to each side of the machinery space. |
26 | In ships certificated to carry more than 12 passengers, the machinery spaces bilge water drainage shall be such that the spaces, where practicable, can be pumped out after a casualty, whether the ship is upright or listed. |
27 | For ships referred to in item 26 there shall be a direct bilge suction pipe from each independent bilge pump situated in the machinery spaces except that not more than two direct suction pipes, one on the port side and one on the starboard side, are required to be fitted in each machinery space. |
28 | Bilge suction pipes shall lead to the forward sides of the machinery spaces where the bilge-water normally drains forward. |
29 | Where a considerable quantity of cooling water is discharged to the machinery space bilges, means shall be provided to deal with that water in addition to the normal bilge-pumping arrangements where the normal bilge-pumping capacity is inadequate to deal with the additional water. |
30 | Where there are depressions in the tank tops due to inverse camber, double bottom discontinuity or accommodation for machinery, means shall be provided to remove bilge-water accumulation in the depressions. |
31 | Where the main propulsion system is electrical, means shall be provided to prevent accumulation of bilge-water under the main propulsion generators and motors. |
32 | Where a machinery space is divided by watertight bulkheads so as to separate the boiler rooms or auxiliary engine rooms from the main engine room, the number and position of the branch bilge suction pipes in the boiler rooms or auxiliary engine rooms shall be the same as for cargo holds referred to in item 49 except that an additional independent power pump direct bilge suction pipe shall be fitted in each watertight compartment and shall, if practicable, lead to the end of the compartment opposite the branch suction pipe location. |
33 | Provisions similar to those set out in item 32 shall be made in each separate motor room of electrically propelled ships. |
34 | The shaft tunnel aft well suction pipe shall be directly connected to the main bilge suction pipe. |
35 | Where the tank top in the shaft tunnel slopes down from aft to forward, a bilge well shall be provided at the forward end of the tunnel in addition to the aft well referred to in item 34 and one suction pipe may serve both wells if the wells are fitted with separate valves. |
36 | Suction pipes for normal bilge pumping in machinery spaces and shaft tunnels shall lead from easily accessible mud boxes fitted with
|
37 | Subject to item 38, strainers shall not be fitted to the lower ends of tailpipes. |
38 | In the case of ships with open floors, strainers with an open area at least three times the area of the suction pipe may be fitted at the lower ends of tail pipes in lieu of mud boxes if the strainers can be fitted in readily accessible locations. |
39 | Bilge cocks, valves and mud boxes shall be fitted at or above the machinery space and shaft tunnel platforms. |
40 | Where it is not practicable to avoid locating bilge cocks, valves and mud boxes at the engine control platform or in passageways, the bilge cocks, valves and mud boxes may be situated just below the platform if readily removable traps or covers are fitted with name-plates indicating the presence of components. |
Emergency Bilge Pumping of Machinery Spaces | |
41 | In addition to the bilge suction pipes required for normal bilge pumping referred to in items 21 to 40, every machinery space shall be fitted with an emergency bilge suction pipe which pipe shall be
|
42 | Where two or more cooling-water pumps are provided, each capable of supplying cooling water for normal propulsion power, only one pump is required to be fitted with an emergency bilge suction pipe. |
43 | In ships with steam-propelled machinery, the emergency bilge suction pipe shall have a diameter of at least two-thirds that of the cooling-water suction pipe connection to the pump, and in other ships, the emergency bilge suction pipe shall have the same diameter as the cooling-water suction pipe connection to the pump. |
44 | Where the main cooling-water pump referred to in subitem 41(a) is less suitable than other available pumps for bilge pumping duties, an emergency bilge suction pipe separate from, and additional to, any other required bilge suction pipe shall be fitted to draw water from the drainage level of a machinery space, and shall
|
45 | Except in ships certificated to carry more than 12 passengers, a direct bilge suction pipe on the same side of the ship as the emergency suction pipe may be omitted where the emergency bilge suction pipe is connected to a self-priming type of pump. |
46 | Emergency bilge suction valve name-plates shall be permanently marked “For emergency use only”. |
47 | A flexible suction hose that has a strainer attached to its lower end and that is of sufficient length and diameter that it is capable of being connected to the suction side of an independent power pump shall be located in the boiler room of every coal-burning ship. |
Bilge Pumping of Cargo Holds, Tanks and Other Non-machinery Spaces | |
48 | An efficient pumping system shall be fitted with bilge suction pipes at suitable drainage levels and located so that all water within any compartment, other than spaces permanently appropriated for the carriage of oil, fresh water or other liquids, can be pumped out through at least one suction pipe when the ship is on an even keel and is either upright or is listing by not more than 5°. |
49 | For the purposes of item 48, suction pipes on each side of the ship are necessary, except in short narrow compartments where one suction pipe can provide effective drainage under the conditions set out in that item. |
50 | In ships certificated to carry more than 12 passengers, the drainage flow arrangements to bilge suction pipes shall be such that all watertight compartments, where practicable, can be pumped out after a casualty, whether the ship is upright or listing. |
51 | The open ends of bilge suction pipes in holds and other compartments outside machinery spaces and shaft tunnels shall be enclosed in strainers that
|
52 | Where, due to size or location of a particular compartment, the installation of a bilge suction pipe would be impracticable, and where flooding calculations indicate that the safety of the ship will not be impaired, the installation of a bilge suction pipe is not required to be installed in that compartment. |
53 | Subject to item 118, in ships that have only one cargo hold, where the cargo hold is over 30 m in length bilge suction pipes shall lead to suitable positions in the aft half length and in the forward half length of the cargo hold. |
54 | Where close-fitting ceilings or continuous plates are fitted over side bilges, arrangements shall be made so that water in a hold compartment can find its way to the bilge suction pipes. |
55 | Where the inner bottom plating extends to the side of the ship, the bilge suction pipes shall lead to wells placed at the side, and if the tank top plating has inverse camber, a suction pipe shall also lead to a well fitted at the centre line of the ship. |
56 | Bilge wells shall have a capacity of not less than 150 L, except that in small compartments bilge wells are not required to be fitted if the bilge suction pipes have steel strainers fitted at their lower end. |
57 | Where access openings to bilge wells are necessary, they shall be fitted as near to the suction strainers as practicable. |
58 | Access to the bilge suction strainer of a bilge well shall not be by means of an opening in machinery space or shaft tunnel watertight divisions, except that where such an arrangement is necessary due to the design features and location of the bilge well, the watertight access opening cover shall be of the hinged type, and a permanent metal plate that bears a notice that the cover must be kept closed, except when access is necessary, shall be affixed in a well-lighted position. |
59 | In ships certificated to carry more than 12 passengers, an access opening shall not pass through the machinery space or shaft tunnel watertight divisions. |
60 | Subject to item 61, the integrity of machinery space or shaft tunnel watertight divisions shall not be impaired by fitting scupper pipe discharges into machinery spaces or shaft tunnels from adjacent compartments situated below the bulkhead deck. |
61 | Scupper pipes with valves and that lead from adjacent compartments may be fitted and lead into a strongly constructed scupper drain tank situated in a machinery space or tunnel. |
62 | The scupper drain tank shall be entirely closed and shall be
|
63 | Means shall be provided for determining the level of water in the scupper drain tank. |
64 | Where one drain tank is used for the drainage of several watertight compartments, the scupper pipes shall be fitted with screw-down non-return valves. |
65 | Means shall be provided for the efficient drainage of the inside of all refrigerated spaces in accordance with rules or codes. |
66 | Means shall be provided for the drainage of the chain locker and watertight compartments above the forepeak tank by manual or power pumps. |
67 | Steering gear compartments or other small enclosed spaces situated above the afterpeak tank shall be provided with suitable means of drainage by manual or power pumps. |
68 | Where the compartments referred to in item 67 are adequately isolated from the adjacent ‘tween-decks, they may be drained by scupper pipes of not less than 35 mm internal diameter discharging to the shaft tunnel, or to machinery spaces in the case of ships with machinery aft, if the pipes are fitted with self-closing cocks situated in well-lighted and visible locations. |
69 | In ships certificated to carry more than 12 passengers, the scupper pipe arrangement referred to in item 68 shall not be fitted unless flooding calculations indicate that the safety of the ship will not be impaired. |
Forepeak and Afterpeak Pumping | |
70 | Where the forepeak and afterpeak are used as tanks, a separate power pump suction pipe shall lead to each tank, except that in the case of small tanks used for the carriage of domestic fresh water, manual pumps may be used. |
71 | Where the forepeak and afterpeak are not used as tanks and power bilge pumping system suction pipes are not fitted, pumping of both peaks may be effected by manual pumps if the suction lift is within the capacity of the pumps and does not exceed 7.5 m in height. |
72 | The collision bulkhead may be pierced by pipes for tank filling and emptying purposes but no open-ended drain valve or cock shall be fitted. |
73 | The pipes referred to in item 72 shall be provided with screw-down valves that are secured to the bulkhead inside the forepeak and that are
|
74 | In ships certificated to carry 12 passengers or less, valves referred to in item 73 may be fitted on the aft side of the collision bulkhead and the valves are not required to be capable of remote control if
|
Watertight Division Components | |
75 | No open-ended drain valve or cock shall be fitted to any watertight division where alternative means of drainage are practicable. |
76 | Where fitted, open-ended drain valves and cocks shall be
|
77 | Valves, cocks, pipes or other components attached directly to the plating of tanks and to watertight divisions shall be secured by
|
Tank Venting Pipes | |
78 | Vent pipes shall be provided for tanks intended to contain liquid. |
79 | Vent pipes shall be arranged to be self-draining when the ship is on an even keel. |
80 | Vent pipes shall be arranged, and the upper part of tanks designed, so that air or gas can freely evacuate. |
81 | Vent pipes shall be fitted at the highest parts of the tanks and, where possible, opposite the filling pipes, when the ship is to be on an even keel. |
82 | When the tank top is of irregular form, the number and location of vent pipes shall be such as to permit the efficient ventilation of the tank. |
83 | Where only one vent pipe is provided, it shall not be used as a filling pipe. |
84 | Vent pipes from double-bottom tanks, deep tanks and other tanks that can be filled from the sea shall lead to above the freeboard deck. |
85 | Vent pipes from compartments such as cofferdams and from all tanks that can be pumped shall not lead to enclosed areas of the ship. |
86 | Means shall be provided to prevent over-pressure or a vacuum in the tanks when closing appliances are in place, by a hole approximately 10 mm in diameter, or other suitable means, in the closing appliance or vent pipe bend. |
87 | In each tank that is capable of being pumped up and in which no over-flow pipe is fitted, the total cross-section of vent pipes shall not be less than 1.25 times the cross-sectional area of the corresponding filling pipes and the internal diameter shall not be less than 50 mm. |
88 | Vent pipes from heeling or trimming pumping system tanks shall be of sufficient size to prevent the tanks from being subjected to a vacuum or over-pressure beyond the designed structural strength of the tanks when the systems are in operation. |
89 | Permanent name-plates shall be attached to the upper part of vent pipes. |
Overflow Pipes | |
90 | Where necessary, overflow pipes shall be fitted to prevent tanks from being subjected during filling operations to pressures greater than test pressures. |
91 | Overflow pipes shall be fitted where the cross-section of the vent pipes is less than that set out for vent pipes in item 87. |
92 | Overflow pipes shall have name-plates attached to the upper part and shall be led
|
93 | Where overflow pipes from tanks containing the same liquid or from tanks each of which contains a different liquid are connected to a common piping system, provision shall be made to prevent any risk of intercommunication between the tanks while the tanks are being emptied or filled. |
94 | Arrangements shall be made so that a tank cannot be flooded from the sea through the overflow pipe where another tank connected to the same overflow pipe system is bilged. |
95 | Overflow piping systems shall be so arranged as to be self-draining when the ship is on an even keel. |
96 | The internal diameter of overflow pipes shall not be less than 50 mm. |
Sounding Arrangements | |
97 | Means shall be provided for sounding all tanks and the bilges of those compartments which are not readily accessible and the soundings shall be taken as near to the suction pipes as practicable. |
98 | Bilges of compartments that are not readily accessible shall be fitted with sounding pipes. |
99 | Sounding pipes shall have an identifying name-plate attached to the upper end, be as straight as practicable, and if curved to suit the structure of the ship, the curvature shall be sufficiently easy to permit the ready passage of the sounding rod or chain. |
100 | Suitable sounding devices may be used in lieu of sounding pipes for tank liquid level gauging if a supplementary means of manual sounding is provided. |
101 | Subject to items 102 and 104, sounding pipes shall lead to locations above the bulkhead deck that are accessible at all times. |
102 | In machinery spaces and shaft tunnels where it is not practicable to extend the sounding pipes from double-bottom tanks to above the bulkhead deck, short sounding pipes extending to readily accessible locations at the lowest working-level platform may be fitted. |
103 | Short sounding pipes to water tanks shall be fitted with shut-off cocks or with screw caps attached to the pipes by chains. |
104 | In ships certificated to carry more than 12 passengers, short sounding pipes may be fitted to cofferdams and double-bottom water tanks situated in the machinery spaces only and shall in all cases to be fitted with self-closing cocks. |
105 | Sounding pipes with elbows shall not be fitted to deep tanks unless the pipes and elbows are situated within closed cofferdams or within tanks containing liquids similar to the liquids in the pipes and elbows, but sounding pipes with elbows may be fitted to tanks other than deep tanks and may be used for sounding compartment bilges if it is not practicable to lead sounding pipes directly to the tanks or compartments. |
106 | The elbows of sounding pipes shall be of heavy construction and adequately supported. |
107 | In ships certificated to carry more than 12 passengers, sounding pipes with elbows shall not be fitted. |
108 | Striking plates of adequate thickness and size shall be fitted under open-ended sounding pipes. |
109 | Where slotted sounding pipes having closed ends are used, the closing plugs shall be of heavy construction. |
110 | The internal diameter of sounding pipes shall be not less than 30 mm. |
111 | All sounding pipes for compartments or tanks that pass through refrigerated spaces, or the insulation thereof, and in which the temperature is 0°C or below, shall be suitably insulated and the internal diameter of the pipes shall not be less than 65 mm. |
Bilge Piping | |
112 | Subject to items 113 to 118 and to items 7 and 8 of Division VI, the internal diameter of main and branch bilge suction pipes shall be in accordance with rules or codes. |
113 | For all ships certificated to carry more than 12 passengers that have a subdivision load line, the diameter of the main bilge pipe shall not be less than that derived in accordance with the following formula, taken to the nearest 5 mm:![]() where
|
114 | The internal diameter of the main bilge suction pipe shall not be less than that of any branch bilge suction pipe and for Group 1 and 2 ships the internal diameter of the main bilge suction pipe shall not be less than 60 mm. |
115 | The internal diameter of the branch bilge suction pipe shall not be less than 50 mm and is not required to be more than 100 mm except in the case of pumping from small spaces, where piping with a diameter of 35 mm or more may be used. |
116 | The internal diameter of the bilge suction pipe to the shaft tunnel well shall not be less than 60 mm except in ships not exceeding 61 m in length, where the internal diameter may not be less than 50 mm. |
117 | Notwithstanding item 114, for ships not exceeding 31 m in length certificated to operate on Minor Waters, Inland Waters Class II or Home Trade Class IV voyages, the diameter of the main and branch bilge suction pipes may be reduced by 20 per cent below the diameter determined in accordance with item 112, but the internal diameter shall not be less than 35 mm. |
118 | For a Group 3 ship that has only one cargo hold, where the hold is over 30 m in length one branch suction pipe only may lead to each side of the after end of the cargo hold if the ship
|
119 | The diameter of the branch suction pipe referred to in item 118 shall not be less than that derived in accordance with the following formula, taken to the nearest 5 mm:![]() where:
|
120 | Where the branch suction pipe referred to in item 118 is used only for the purpose of pumping from the cargo hold, it may be connected to the main bilge pipe or the main ballast pipe, but in such a case
|
121 | Where the branch suction pipe referred to in item 118 is used for the purpose of pumping from and filling the cargo hold, it shall be connected to the main ballast pipe, and in such case
|
122 | The cross-sectional area of each pipe connecting the main bilge pipe to a bilge distribution manifold shall not be less than the sum of the cross-sectional areas of the two largest branch bilge suction pipes connected to the manifold, but need not be greater than the cross-sectional area of the main bilge pipe. |
123 | Subject to item 124, the diameter of direct bilge suction pipes in machinery spaces, other than emergency suction pipes, shall have a diameter not less than the diameter of the main bilge pipe. |
124 | For Group 3 ships, where direct bilge suction pipes lead to both sides of the ship for normal bilge pumping, one suction pipe shall be of a size not less than that of the main bilge pipe and the other suction pipe may be of the size of the machinery space branch bilge suction pipe, but the smaller suction pipe shall be fitted on the same side as the emergency bilge suction pipe. |
Bilge Pumps and Connections | |
125 | All power pumps essential for bilge pumping shall be of the self-priming type unless a central priming system is provided for those pumps. |
126 | Each power bilge pump shall be capable of giving a flow rate of water through the required main bilge pipe of not less than 2 m/s as set out in the Table of Capacities to this Part. |
127 | Bilge pumps may be used as fire pumps if the simultaneous operation of bilge-pumping systems and fire-pumping systems is not compromised. |
128 | Sanitary, ballast and general service pumps may be used as independent power bilge pumps if they are fitted with the necessary connections for bilge pumping. |
129 | No emergency bilge pump shall be installed forward of the collision bulkhead. |
130 | Pumps required for essential services shall not be connected to a common suction manifold, a common suction pipe, a common discharge manifold or a common discharge pipe unless the arrangements are such that the working of any pump so connected will not be affected by any other pumps operating at the same time. |
131 | Bilge pumps shall have isolating valves so that any one pump may continue to operate when another pump is dismantled. |
132 | Where relief valves are fitted to bilge pumps that have sea connections, those valves and their outlets shall be fitted in readily visible locations above the lowest working-level platform. |
133 | In ships certificated to carry more than 12 passengers, power bilge pumps located in spaces other than machinery spaces are required to have separate direct suction pipes unless the size of the other spaces does not warrant such pipes. |
DIVISION IIIGroup 1 Ships
Item | Requirements |
---|---|
Bilge Pumps and Connections | |
1 | The main bilge pipe shall be connected to
|
2 | One of the power pumps referred to in item 1 may be directly driven by a main propulsion engine. |
DIVISION IVGroup 2 Ships
Item | Requirements |
---|---|
Bilge Pumps and Connections | |
1 | The main bilge pipe shall be connected to
|
2 | One of the power pumps referred to in item 1 may be directly driven by a main propulsion engine. |
3 | In ships of less than 91.5 m in length certificated to operate on Minor Waters Class I voyages, the number of pumps set out in item 1 may be reduced by one. |
4 | In ships of less than 61 m in length certificated to operate on voyages other than Minor Waters Class I voyages, the number of pumps set out in item 1 may be reduced by one if one manual pump having inlet and outlet sizes equal to or greater than those of the pump it is replacing is provided. |
DIVISION VGroups 1 and 2 Ships
Item | Requirements |
---|---|
1 | In ships of 91.5 m or more in length, or that have a Criterion of Service Numeral for the ship, as determined pursuant to the Hull Construction Regulations, of 30 or more, the bilge pumping system shall have at least one power pump available for use in all flooding conditions the ship is designed to withstand. |
2 | The requirement of item 1 is met where
|
3 | Controls referred to in subitem 2(a) shall be clearly identified and an indication of their operational status at the remote control location given, and where extended spindles are used for valves, the spindles shall lead as directly as possible to the remote control location. |
4 | Where the ship is not a Safety Convention ship, one power pump, other than the emergency pump, with a pumping capacity of not less than 70 per cent of the capacity set out in the Table of Capacities to this Part may be used where the deficiency in pumping capacity is made up by the excess capacity in the other power pumps. |
5 | The required power pump capacity in m3 per hour for a given internal diameter in millimetres of main bilge pipes is set out in the Table of Capacities to this Part. |
6 | Where practicable, the power bilge pumps shall be placed in separate watertight compartments so arranged or situated that those compartments will not readily be flooded by the same casualty. |
7 | Where the engines and boilers are in two or more watertight compartments, the pumps available for bilge service shall be distributed throughout the compartments to the extent possible. |
8 | Manual bilge pumps, where fitted, shall be operable from above the bulkhead deck and shall be so arranged that the components can be withdrawn for examination and overhaul during flooding. |
9 | Where two manual pumps are fitted, a shut-off valve or cock operated from above the bulkhead deck, or non-return valves, shall be fitted to enable one of the pumps to be dismantled without the efficiency of the other being affected. |
10 | In coal-burning ships where there is no watertight bulkhead between the engine room and the boiler room, a direct discharge overboard shall be fitted from at least one condenser circulating water pump, or a condenser by-pass shall be fitted to the circulating water pipeline. |
11 | The main bilge pipe shall be arranged so that no part is situated nearer the side of the ship than the B/5 line where B is the breadth of the ship measured at right angles to the centre line at the level of the deepest subdivision load line or deep load line where a subdivision load line is not assigned. |
12 | Where any bilge pump or its connecting pipe to the main bilge pipe is situated outboard of the B/5 line,
|
13 | Means shall be provided to prevent the compartment served by any bilge suction pipe from being flooded in the event of the pipe being severed or otherwise damaged in any other compartment by collision or grounding. |
14 | For the purpose of item 13, where any part of a bilge suction pipe is situated outboard of the B/5 line or in a duct keel, a non-return valve shall be fitted to the pipe in the compartment containing an open end. |
15 | All distribution boxes, cocks and valves in bilge pumping systems shall be
|
16 | Where there is only one system of pipes common to all the bilge pumps, the necessary cocks or valves for controlling the bilge suction shall be operable from above the bulkhead deck. |
17 | Where, in addition to the main bilge pumping system, an emergency bilge pumping system is fitted,
|
18 | Remote controls for cocks and valves referred to in subitem 17(b) shall lead as directly as possible to the remote control location and shall be clearly identified at the upper end and an indication of their operational status given. |
19 | Where divided deep tanks or side tanks are provided with cross-flooding arrangements to limit the angle of heel after side damage, the arrangements shall be self-acting where practicable. |
20 | In the case where cross-flooding controls are necessary, such controls shall be clearly identified and shall be operable from above the bulkhead deck. |
21 | The size of vent pipes for tanks fitted with cross-flooding connections shall be determined by the size of the cross-flooding connections. |
22 | There shall be no closing appliance on vent pipes of tanks fitted with cross-flooding connections. |
DIVISION VIGroup 3 Ships
Item | Requirements |
---|---|
1 | The main bilge pipe shall be connected to at least two power pumps. |
2 | Two power pumps operating together may be used in lieu of one power pump if the pumps have at least a combined capacity equivalent to the one power pump. |
3 | For ships not exceeding 91.5 m in length, one of the power pumps required by item 1 may be driven directly by the main propulsion engine. |
4 | For ships not exceeding 150 tons gross tonnage certificated to operate on Minor Waters, Inland Waters Class II or Home Trade Class IV voyages, a manual pump may be used in lieu of a power pump if it has inlet and outlet sizes equal to or greater than those of the power pump. |
5 | One power pump with a pumping capacity of not less than 70 per cent of the capacity set out in the Table of Capacities to this Part may be used where the deficiency in pumping capacity is made up by the excess capacity in the other power pumps. |
6 | The power pump capacity in m3 per hour for a given internal diameter in millimeters of main bilge pipes is set out in the Table of Capacities to this Part. |
Oil Tankers and Similar Ships | |
7 | For oil tankers and similar ships where the main machinery space bilge pumps are not connected to bilge pumping systems outside the machinery space, a main bilge suction pipe that has a cross-sectional area of not less than twice that of the branch bilge suction pipe may be used. |
8 | Design of bilge-water pumping systems outside the main machinery space and of ballast water systems in oil tankers and similar ships referred to in item 7 shall be in accordance with rules or codes. |
DIVISION VIIGroup 4 Ships
Item | Requirements |
---|---|
Piping Systems | |
1 | An effective pumping system shall be fitted with bilge suction pipes leading to drainage levels that permit all water within any compartment or any watertight section of any compartment to be pumped out through at least one suction pipe when the ship is on an even keel and is either upright or is listing by not more than 5°. |
2 | In ships certificated to carry more than 12 passengers, bilge water drainage in machinery spaces and watertight compartments shall be such that the spaces and compartments, where practicable, can be pumped out after a casualty when the ship is upright or listing. |
3 | The arrangement of the pumping system shall be such as to prevent the possibility of water passing from the sea to any compartment or from one watertight compartment to another and for that purpose bilge suction valves shall be of the screw-down non-return type. |
4 | A machinery space bilge suction pipe shall lead from an easily accessible mud box that is fitted with a straight tailpipe to the bilge, except that a mud box is not required if the tailpipe leads to an easily accessible strainer that has a total open area of at least three times the cross-sectional area of the suction pipe. |
5 | The open ends of bilge suction pipes in compartments outside machinery spaces shall be enclosed in strainers that
|
6 | Bilge suction pipes shall have an internal diameter of not less than 35 mm, except that ships not in excess of 11 m in length may have suction pipes with an internal diameter of not less than 25 mm. |
7 | Subject to item 2, where a ship is not in excess of 11 m in length, one machinery space bilge suction pipe only is required to be fitted. |
8 | Bilge suction pipes for pumping cargo or machinery spaces shall be entirely separate from sea inlet pipes that may be used for filling or emptying spaces where liquid is carried. |
9 | Sea suction, overboard discharge and bilge valves shall be in easily accessible locations and readily visible. |
10 | Pipes shall be made in readily removable lengths with flanged joints, or other connections of a type offering security equivalent to that of flanged joints. |
Pumps | |
11 | The bilge suction pipe shall be connected to at least two pumps of the self-priming type unless a central priming system is provided for the pumps. |
12 | At least one bilge pump shall be an independent power pump and the other bilge pump may be a main propulsion engine-driven pump or manual pump, if the pumping capacity of each power pump meets the requirements of the Table of Capacities to this Part and the manual pump has inlet and outlet sizes equal to or greater than those of the independent power bilge pump. |
13 | For ships certificated to operate on Minor Waters, Inland Waters Class II and Home Trade Class IV voyages, each power pump capacity may be reduced by 20 per cent of the capacity set out in the Table of Capacities to this Part, but there shall be no reduction in the piping diameter. |
14 | For ships in excess of 11 m in length, the independent power pump shall have, in addition to the main bilge suction pipe connection, a direct machinery space bilge suction pipe of equal diameter. |
15 | Bilge pumps may be used as fire pumps if the simultaneous operation of bilge-pumping systems and fire-pumping systems is not compromised. |
16 | A general service power pump that is not connected to oil systems may be used as an independent bilge pump if it is fitted with the necessary connections for bilge pumping. |
17 | Pumps shall have isolating valves so that any one pump may continue to operate when another pump is dismantled. |
DIVISION VIIIGroup 5 Ships
Item | Requirements |
---|---|
Piping Systems | |
1 | An effective pumping system shall be fitted with bilge suction pipes leading to drainage levels so that all water within any compartment can be pumped out through at least one suction pipe when the ship is on an even keel and is either upright or is listing by not more than 5°. |
2 | The arrangement of the pumping system shall be such as to prevent the possibility of water passing from the sea to any compartment or from one watertight compartment to another. |
3 | Bilge suction pipes with effective strainers shall have an internal diameter of not less than 25 mm. |
Pumps | |
4 | The bilge pumping system shall have at least two effective bilge pumps. |
5 | Subject to items 6 to 8, at least one bilge pump shall be a power pump and the other bilge pump may be a manual pump if the pumping capacity of the power pump meets the requirements of the Table of Capacities to this Part and the manual pump has inlet and outlet sizes equal to or greater than those of the power pump. |
6 | For a passenger launch in excess of 18 m in length, both pumps shall be power pumps, one of which may be main propulsion engine-driven. |
7 | For a ship or launch not in excess of 11 m in length certificated to operate on Home Trade Class IV or Minor Waters Class II voyages,
|
8 | The main propulsion engine cooling-water system may be adapted for bilge pumping and used in lieu of the manual pump referred to in item 5 if
|
9 | Bilge pumps may be used as fire pumps if the simultaneous operation of bilge-pumping systems and fire-pumping systems is not compromised. |
10 | A general service power pump that is not connected to oil systems may be used as an independent bilge pump if it is fitted with the necessary connections for bilge pumping. |
11 | Pumps shall have isolating valves so that any one pump may continue to operate when another pump is dismantled. |
12 | For ships for which plans are not required to be submitted, the arrangement and capacity of the bilge pumping system shall be suitable for the type, service and voyages of the ship. |
Table of Capacities
Pumping Capacities for a Flow Rate of 2 M/S
Internal diameter of bilge pipe in mm | Capacity of each power pump in m3 per hour |
---|---|
25 | 3.5 (58 L/min) |
32 | 5.8 (96 L/min) |
38 | 8.2 (136 L/min) |
51 | 14.7 (245 L/min) |
57 | 18.4 |
64 | 23.2 |
70 | 27.7 |
76 | 32.7 |
83 | 39.0 |
90 | 45.8 |
95 | 51.0 |
102 | 58.8 |
108 | 66.0 |
114 | 73.5 |
121 | 82.8 |
127 | 91.2 |
133 | 100.0 |
140 | 110.8 |
146 | 120.5 |
152 | 130.6 |
159 | 143.0 |
165 | 154.0 |
171 | 165.3 |
178 | 179.2 |
184 | 191.4 |
191 | 206.3 |
197 | 219.5 |
203 | 233.0 |
210 | 249.4 |
PART II(Section 6)Plans
Item | Information Required |
---|---|
1 | General arrangement and location of bilge, ballast, heeling, trimming and passive roll stabilizing systems, including venting, overflow and sounding arrangements, showing all connected piping, valves, pumps and equipment, emergency systems and cross-connections to other fluid systems. |
2 | Installation details stating assigned working pressures and flow rates of fluid and, where applicable, the Criterion of Service Numeral of the ship, as determined pursuant to the Hull Construction Regulations. |
3 | Materials, sizes, capacities, design working pressures, testing arrangements and procedures of pumps, valves, piping, any tank sounding and venting devices. |
4 | Details of
|
5 | Information set out in items 2 to 4 is not required to be submitted for ships not in excess of 18 m in length. |
6 | Information for valves and similar minor components referred to in item 3 is not required to be submitted where a manufacturer or an approved classification society certifies that the types of valves or similar minor components have been designed and constructed in accordance with rules or codes. |
7 | Information for pumps referred to in item 3 is not required to be submitted where an approved classification society certifies that the pumps have been designed and constructed in accordance with rules or codes except that the driving motor or engine of pumps shall meet the requirements of Part II of the applicable schedule of Schedules I to XV. |
PART III(Subsection 12(2))Construction and Installation Inspections
DIVISION IConstruction inspection
Item | Requirements |
---|---|
1 | None. |
DIVISION IIInstallation inspection
Item | Requirements |
---|---|
1 | Identification from component inspection certificates, before installation is commenced, of pumps, any tank sounding and venting devices, flexible hoses, materials, welding metal, other components and harmful substances discharge prevention equipment to be used. |
2 | Verification that welding was carried out by welders certified by a Provincial Government of Canada, or another authority having similar standards where the welding was carried out outside Canada, for the class of work to be done. |
3 | Inspection of welds. |
4 | Witnessing of hydrostatic pressure tests in accordance with rules or codes, including hydrostatic pressure test of bilge suction pipes through double bottom tanks to the same pressure as the tanks through which they pass. |
5 | Inspection of securing arrangements, connection of bilge and ballast pumping systems and heeling, trimming and passive role tank filling and emptying systems to associated systems and verification of correct adjustment and operational condition of safety, control and monitoring devices. |
6 | Witnessing of operational tests of the system in accordance with rules or codes. |
PART IVPeriodic General Inspections and Periodic Special Inspections
DIVISION I(Section 19)Periodic General Inspection
Item | Requirements |
---|---|
1 | Where applicable and, in the opinion of the inspector, practicable,
|
DIVISION IIPeriodic Special Inspection
SUBDIVISION I(Subsection 20(1))Parts to be Inspected
Item | Requirements |
---|---|
1 | External and internal parts of pump and driving components including valves, controls and safety devices. |
2 | External and internal parts of bilge valves including emergency bilge suction valves, mud boxes and strainers. |
3 | Securing arrangements, without dismantling if a general examination shows that the condition of the components is suitable for further service. |
4 | No inspection is required for complex mechanisms where written information is provided to the inspector from firms specializing in the reconditioning of these parts indicating that the parts are in good order and adjustment. |
SUBDIVISION II(Subsection 20(2))Intervals
Item | Requirements |
---|---|
1 | At intervals not exceeding five years. |
- SOR/2015-161, ss. 34(E), 35 to 38(F), 39(E), 40(E), 41(F), 42(E), 43(E), 44 to 50(F), 51, 52 to 54(F)
SCHEDULE XVI(Section 4)
General Design Specifications
Item | Requirements |
---|---|
1 | For ships operating in extremely cold conditions, the design of all essential liquid or steam systems prone to frost damage or operational impairment shall take into account those operational conditions and the low-temperature characteristics of CO2 and any other gases to be used in a ship system. |
2 | Water piping systems intended for use in areas exposed to freezing conditions shall, as far as practicable, be separate from water systems intended for use in internal spaces of ships, with drainage facilities being fitted in suitable and easily accessible locations. |
3 | Materials subjected to stress at high or low temperatures shall be resistant to failure due to such temperatures. |
4 | Means shall be provided to bring into operation propulsion and ship service machinery from a dead ship condition without external aid. |
5 | Machinery shall be protected against overspeeding and excessive vibration. |
6 | Ship propulsion systems shall have sufficient power, and arrangements shall be provided to enable the ship to be manoeuvered both ahead and astern and controlled at sea, having regard to the voyages the ship is to make. |
7 | Normal operation of the propulsion machinery shall be sustainable or restorable where one of the essential auxiliaries becomes inoperative, but a partial reduction in propulsion capability from normal operation is acceptable. |
8 | For single essential propulsion components, means shall be provided to assure reliability, especially in the case of unconventional arrangements. |
9 | All machinery shall be designed to operate when the ship is upright and when listing at any angle up to and including 15° either way under static conditions and 22.5° either way under rolling conditions and simultaneously inclined 7.5° by the bow or stern under pitching conditions. |
10 | Effective guards shall be provided for protection against machinery that moves, is hot or is otherwise hazardous. |
11 | Slip-resisting gratings, handrails and ladders shall be fitted to allow access to machinery for operational and maintenance purposes with particular attention being given to spaces where fluids may leak, such as steering gear compartments. |
12 | Sufficient means shall be provided, including lighting, to inspect, maintain and clean machinery parts. |
13 | Machinery spaces of category A shall be adequately ventilated so that when boilers or other machinery are operating at full power in all weather conditions, an adequate supply of air to the spaces is maintained for the safety and comfort of personnel and the operation of the machinery. |
14 | Other machinery spaces shall be adequately ventilated. |
15 | Where applicable, at least two independent means of communication shall be provided for communicating orders from the bridge to the location in the machinery space, or in the control room, from which the engines are normally controlled, and one of the means of communication shall be an engine-room telegraph that provides visual indication of the orders and responses both in the machinery space and on the bridge. |
16 | Appropriate means of communication shall be provided to any locations other than those referred to in item 15 from which the engines may be controlled. |
SCHEDULE XVII(Sections 9 and 10)
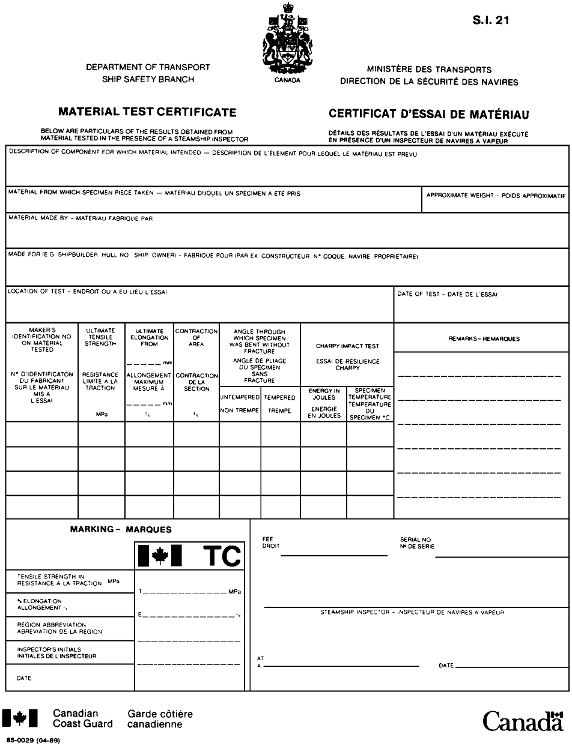
SCHEDULE XVIII(Sections 16 and 24)
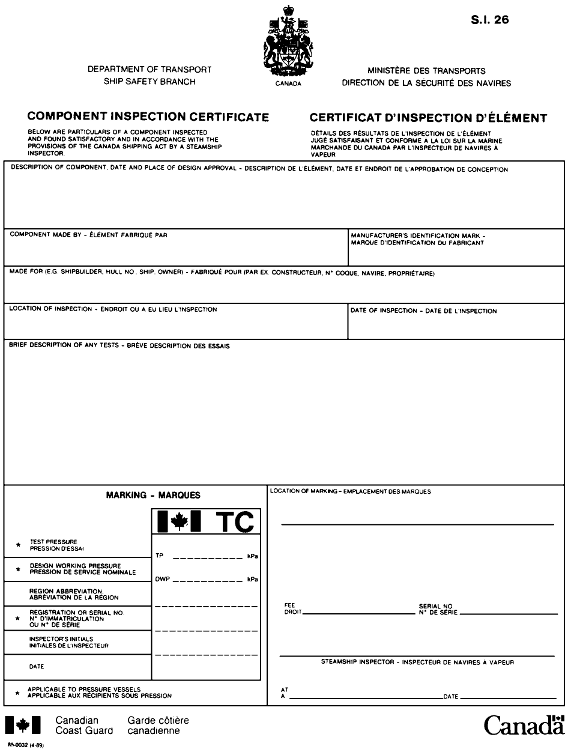
- Date modified: